Life is getting tough for the print business in Surat, but the growth prospect is strong.Progressive Printing Press in Surat says the CMYK colour gamut is narrower than the Adobe RGB colour space available in files and on pre-press monitors.In this Sunday Column, we tell you about how Progressive is using the RGB colour range to its full potential from screen to print
Since 1998, Progressive Printing Press has worked to develop a strong reputation for itself in the Surat’s print industry. The company was established in 1965 using treadle machine initially and then single-colour machines to produce four-colour jobs.
Progressive Printing Press’ owner and managing director Asgar Sanchawala says, he ushered a new era in four-colour offset printing for Progressive when his company installed a used Komori Sprint 425 and a Polar cutting machine in 1998. “It significantly changed the fortunes of the company,” says Sanchawala.
Over the years, the company has evolved. From specialising in magazine, stationery and such kind of jobs to redefining the traditional CMYK colour gamut in partnership with the Japanese manufacturer, Toyo Ink.
Sanchawala says the print industry is made of niches, and when one attains it, people follow and then there’s overkill. That’s when you start looking for the next niche, that something which will add value into our business.
So when Sanchawala’s son Latif wanted to do something new at Progressive, he knew it would be a long drawn affair.
Playing with colours
Progressive had been using GMG Solutions for colour management, using its GMG colour server and GMG ink optimiser since 2013. Latif explains, “The optimiser optimises colour composition of printing data automatically and in a matter of seconds. This significantly improved the printing quality.”
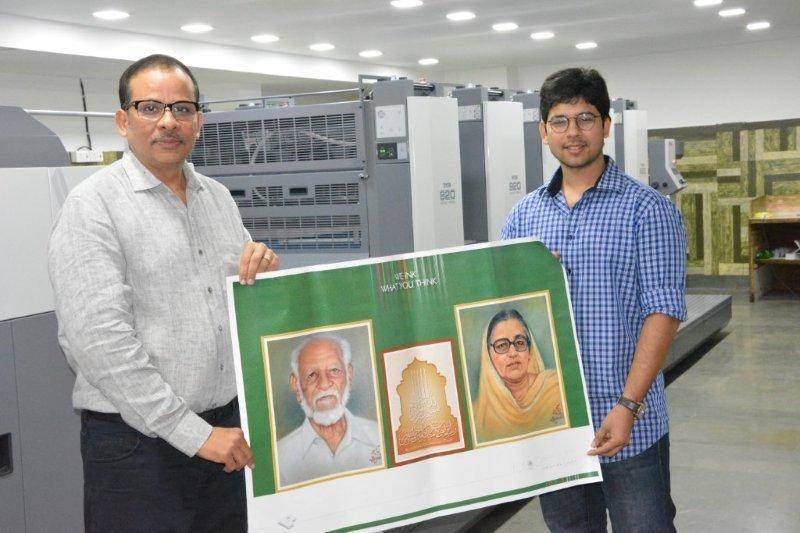
Optimisation is based on GMG’s 4D DeviceLink profiles. The CMY colour component is replaced by black while exactly retaining the colour impression. Sophisticated ink reduction algorithms ensure that only the structure of the separations is altered, not the colour impression. “The improved colour composition makes it possible to stabilise the entire printing process, meaning that, for example, the gray balance reacts less to colour fluctuations. Depending on the printing process and the substrate, GMG ink optimiser simultaneously achieves up to 20% savings on ink,” says Latif.
But he was not satisfied; he wanted to get into hexachrome printing. “I wanted to get out of the status quo. I wanted to do something that will allow us to improve our offering to the customers and productivity.”
"Percept Print Solutions’ Afsal Kottal, the representative for GMG suggested that we try a product from GMG’s sister concern, Coco software." Unfortunately, for Progressive, the experiment did not bear fruit because to do Hexachrome printing the company would have to invest in a six-colour press.
At this point Sanchawala says, he suggested Latif try experimenting with Toyo’s Kaleido. “The president of Toyo, BS Kampani is a close friend, and he helped us get onto this project.”
But reproducing a picture which included colours beyond the CMYK colour space required special arrangements. Printing to an expanded gamut on your press requires several things. It needed a press that could print to higher densities and also software to convert RGB images to CMYK.
The steps of uploading the Kaleido profile as well as printing test chart were done. Progressive, along with teams from Toyo and Percept collaborated. “We needed Percept support because of the black component in the ink. That had to be reduced in the overall Kaleido standard print density, which is on the higher side,” says Latif.
It took six months for the project to become successful and ever since, Progressive has been using Kaleido in almost all its work. “It included stopping of work, few job rejections and bouts of angry words from my dad,” says Latif.
Latif cites an example of a catalogue which he printed for a customer, who he says is not always fixated with a perception of colour. “The customer screamed saying that we have changed the colours of his catalogue. We explained the new process and the ink used. He accepted it, used it for his work and has received a great response.” Since then, the customer has been ordering prints to be executed with Kaleido inks and also pays for it.
In today’s competitive print market quality is most important and to have an edge with the competitor, better colour can make the difference. The Kaleido has helped Progressive to improve the transparency of yellow, magenta and cyan. As a result, magenta and pink hues appear vivid, and blue and red tones are notably improved. The other benefit is superior gloss. “Toyo Kaleido has added the extra punch (colour) to the extraordinary dress material catalogue printed at Progressive Printers,” says Latif.
But are the customers ready to pay, because it’s not just the cost of ink, it’s the quantity of ink that is used. “The consumption of inks is also more while using Kaleido. If you are using one kilogram of normal ink, then we are using 1.5 kg of Kaleido, plus the cost is three times higher,” says Latif, which according to him is a flip side of the project.
Right now, says Latif, the company is only charging the extra cost of the inks. “There is one client who we charge premium right now, but once our prints get acceptance, which is not far away, we will get into the premium mode. I have believed that if you are doing something different, then there are clients who are ready to pay.”
At present, Progressive uses 400kg of Kaleido ink, and hopes to up that once demand increases.
Pre-owned to brand new
Progressive has overhauled its press room. The company has now come to realise that it has to move with the new realities of the print industry in Surat, where the market is now looking to newer things, where one needs to do more with less.
And so began the modernisation of the press room.
Of the pre-owned four-colour presses that the company had invested in, just two remain; a Komori 20x25 and a 28x40in. A new Ryobi 920 has been brought in, which will now become the cornerstone of the company.
“There was a time when I favoured pre-owned press, and while I would still do, the reason I got in Ryobi is because it was the only press that offered a coater in the 25x36in size. It was at least till the time we had placed the order,” says Sanchawala. Since then Komori and Heidelberg have added a coater to its similar sized machines.
Sanchawala added, the 25x36in size with 8-up is a very useful size in the Surat market. “We do design catalogues in this very size. Earlier we used the larger Komori press for this work. So in a way, it has also saved around Rs 1-lakh on plate. We also see the saving on space and staff as profit. According to me, there is around 30% savings.”
The other USP of a new machine is its productivity. At present, the company does 15-18 jobs per day and in the next three months hopes to do 35 jobs in a 12-hour shift. “A brand new machine gives us the advantage of production and we hope that our production will double soon,” says Sanchawala.
Future plans
Sanchawala is aware of the noises made about the LED technology, but is not yet ready for the challenge. Sanchawala says, he will wait for three more years till the technology matures. “We are totally into commercial printing and right now are not targeting any other segment,” says Sanchawala.
During Drupa 2012, Sanchawala invested in the Landa Nanography. “Yes, our deposit is still with the company. But we have also seen other B2 digital options, and I hope to see them at Drupa 2016.”
PASSING THE KALEIDO TEST - LATIF SANCHAWALA
The Progressive team under the guidance of Toyo team led by KS Murthy, Inderjit Singh, Mukesh Ahire and Saorabh Gupta and Dass Damodaran of Percept Print Solution worked on the project.
How Kaleido works
Kaleido works with two components:
-
Kaleido ICC Profile (For converting RGB Images into CMYK)
-
Kaleido Process colour set: (high pigmentation)
Kaleido ICC Profile (For converting RGB Images into CMYK)
Original RGB file: Reproducing a picture which included colours beyond the CMYK colour space requires special arrangements. Printing to an expanded gamut on the press requires several things. Not only must the press be able to print to higher densities but it should also have software to convert RGB images into CMYK.
We cannot use any file in and expect it to show the benefits of the high gamut target you have created. If we just take a CMYK separation and put it into this expanded colour space the results are going to be unimpressive. CMYK to CMYK does not lead to great results and in the world of colour management it is often considered a bad thing to convert between the same colour spaces.
RGB colour space is used in digital printing data, pre-press monitors and digital photography. Since the CMYK colour gamut is narrower than that of the RGB, it is impossible to reach the original RGB colour range.
Hence the need for Kaleido V.5.00 ICC profile in pre-press to convert the original RGB images into CMYK. Toyo Kaleido V5.00.icc is a device profile for offset printing using process colour ink, Kaleido.
Kaleido Process colour set (High pigmentation)
In order to achieve a higher colour space, a printer needs to run higher ink densities, up to 1.70 or 1.80 density, or even higher. There is a limit because at a certain point the ink becomes dirty and colour actually degrades.
Also, the printing process is only designed to use a certain amount of ink film thickness (IFT). Too much ink makes runability out of control. The only way to effectively "push" ink to higher densities and still maintain balance on the press is to mix the ink with a higher pigment load.
Kaleido four CMYK process colours enhances the secondary and tertiary colours, thereby improving the transparency of yellow, magenta and cyan. As a result, magenta and pink hues appear vivid, and blue and red tones are notably improved. The other benefit is superior gloss.
THE PROCEDURE
Step 1
Upload the Kaleido profile in your system
1. The Toyo Kaleido V5.00 ICC profile needs to be uploaded in the operating system either on Mac or Window XP.
2. In Photoshop select CMYK profile as Kaleido V5.00.
3. Open original RGB file.
4. Convert file to CMYK using Kaleido V5.00 ICC profile.
Step 2
Printing Test chart
1. The Kaleido starter kit comes with Test chart and Target Print densities and L,a,b values.
2. The printing density for Kaleido ink is 15% higher than that of normal ink.
3. Print the test chart with Kaleido print density (1.75 cyan, 1.65 magenta, 1.45 Yellow and 1.95 black) for coated substrate.
4. Check the solid part density, Lab, and dot gain value at 50% part.
5. Check the dot gain to make sure that it is not exceeding 70% at 50% dot part. If the dot gain value is not good enough for the Kaleido standard you need to change CTP curve to have a good result.
6. In case that the dot gains value is exceeding 19%, it is recommended to use CTP output adjustment function to reduce the dot gain value by 3% less from an ordinary condition.
7. Reprint the test chart after doing the dot gain compensation in CTP and see if the dot gain is within the limit.
8. Measure the Lab value at the solid parts of CMYK, *RGB, and input such Lab values.
9. Compare the Lab values in above gamut graph with Toyo’s recommended Lab value. If the gamut by the test print is close or larger than Toyo’s recommendation, the printing test conditions are considered usable regardless of the density value.