Flexo pre-press specialists at Labelexpo 2016
When CTP technology was introduced for offset platemaking, all the skill and expertise of creating that perfect dot was reduced to a push of a button. Everyone could create a good quality plate and over a period, the process of platemaking went in-house. Today, even the thermal versus violet CTP debate is a passé.
12 Dec 2016 | By Rushikesh Aravkar
Not so with flexo pre-press. Even with the latest developments in digital flexo pre-press over the last decade, one must agree that pre-press in flexo remains more of an art than of science. It still remains the mastery of a select few.
That’s the reason why Labelexpo 2016 saw more than six flexo pre-press houses flaunting their expertise. These included Ahmedabad-based Ankit Graphics, Hyderabad-based Digiflex, Noida-based Creative Graphics, Bengaluru-based Veepee Graphics, New Delhi-based Alpha Flex and AM Boards.
All these firms have made significant investments in hardware and software and automated operations, anticipating demand for flexographic printing. That’s because label converters are adding capacities, gravure converters are investing in CI flexo presses and more and more gravure jobs are being converted to flexo.
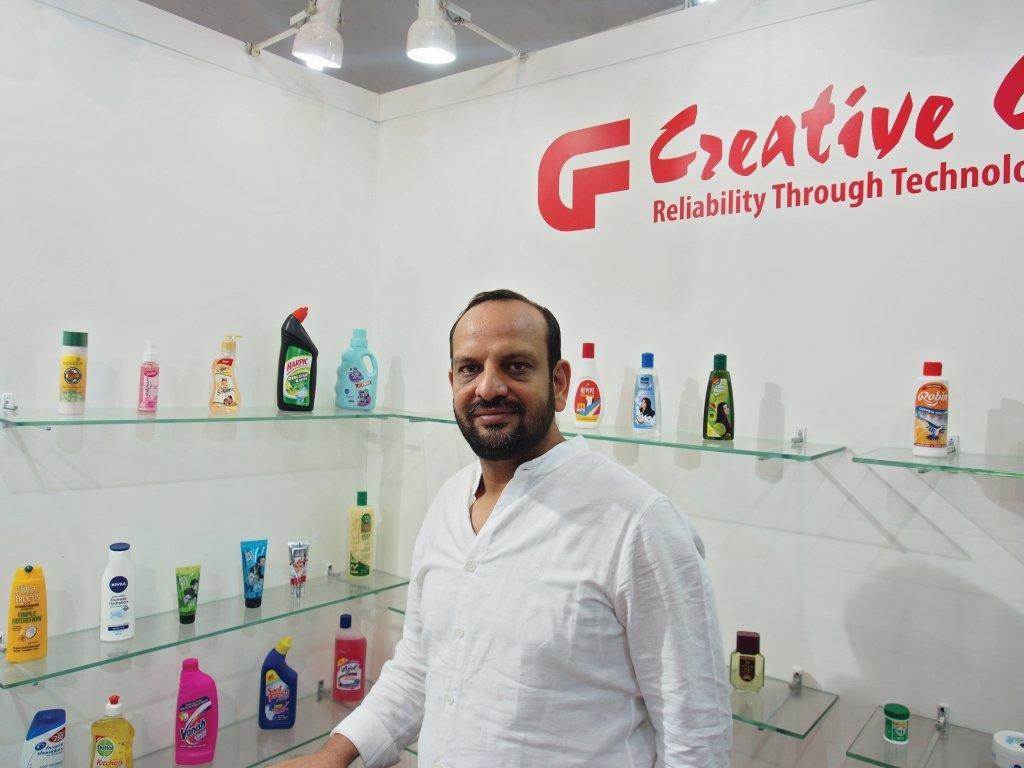
Creative Graphics has been an Esko loyalist right from the beginning. Today, it runs multi-location operations in Noida, Vasai (Mumbai) and Hyderabad. Deepanshu Goel of Creative Graphics says the focus has shifted to faster delivery and finest quality. “Customers are demanding plates in shortest turnaround,” he adds.
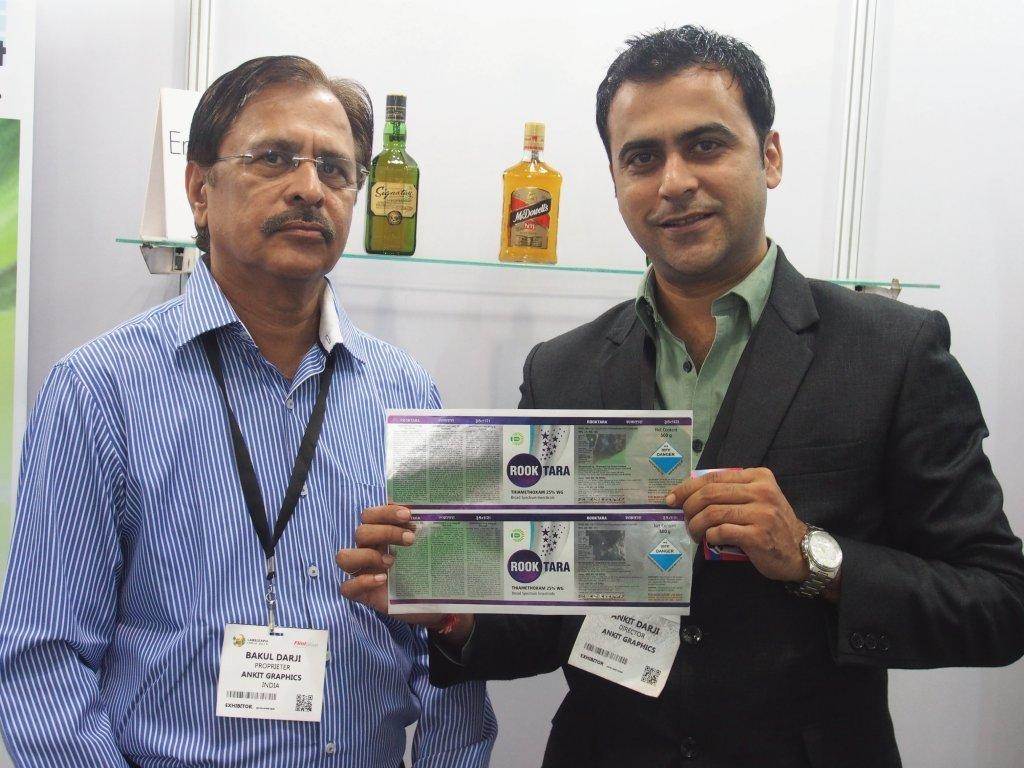
Ankit Graphics, a first-timer at Labelexpo, deploys its Screen Platerite-produced plates to run on Nilpeter and RK Machinery presses. Ankit Darji of Ankit Graphics says, “The accuracy of flexo plates can make or break image quality for a converter. So there’s a huge responsibility that we as a pre-press bureau carry. The response at the show has been impressive. We saw a significant amount of offset printers keen to invest in flexo and labels. It’s good for business.”
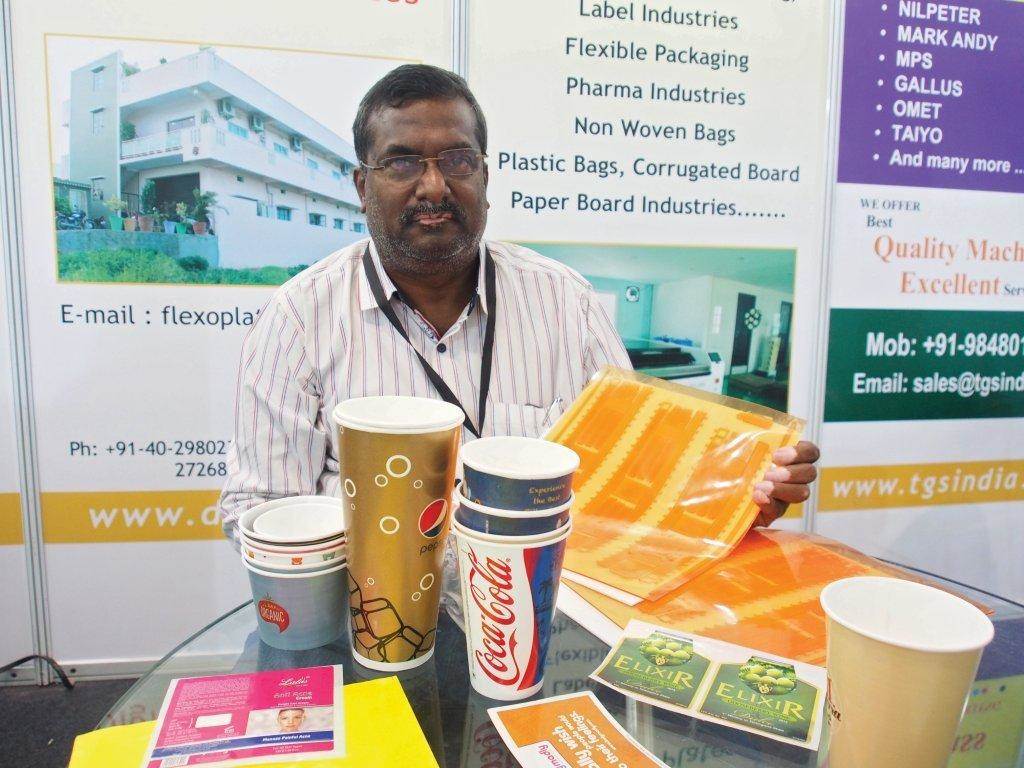
For all the pre-press bureaus, the goal is to help their customer create crisp images that can be produced consistently, again and again. But that’s not all. The customers are looking at productivity improvement by achieving the same quality but with reduced number of colours.The latest entrant, Digiflex, which started operations a year ago with Kodak Flexcel technology, has reported 25% month-on-month increase in the number customers and claims to have captured more than 95% of flexo market in Hyderabad.
Speaking of changing customer needs, Shyam Sunder of Digiflex says, “There is an increase in demand for printing higher density solids without laying down more ink and printing high-density white in a single pass.”
Goel agrees. “It’s a challenge to make the customer understand the process differences between gravure and flexo and why it is difficult to achieve gravure quality on flexo. With the technology available, we try to go as close as possible to gravure quality.”
Sunder adds, “When converting jobs from gravure to flexo, there are some jobs which consume more ink, especially with opaque white. For such jobs, our expertise and intelligent use of hybrid screening is required to ensure that ink densities are kept in check.”
In terms of line screen and dot size, 130-150 lpi and 3% dot is status quo.
Darji says, “Achieving 0.5% dot is possible for both pre-press houses as well as printers, but going for such small dot means drastically reducing the press speed. Also, care needs to be taken to keep the plate clean and avoid ink build-up on that micro dot. This hampers productivity. Hence printers avoid having such fine elements in the artwork.
Both Darji and Goel concede that the label printers today want to print higher line screens. For a converter using UV inks and anilox above 1000 lpi, a plate with 150 lpi works well. “There are customers who demand 1% and 0.5% dot and can print line screens of up to 175 lpi. You need to invest in higher anilox if you want to print higher lpi. The label converters like Ahmedabad-based Nitai Press, Accutech Packaging in Vadodara, and Renault Paper Products in Palghar have good sets of anilox. I supply 175 lpi to these clients,” says Darji.
As the end-customer pushes the envelope further, and the benchmark of quality rises further, and artworks become more complex, the onus of quality production will lie with pre-press bureaus. “1% dot and 175 lpi will soon become industry norm and we will be experimenting with even finer line screens and nano dots soon,” concludes Sunder.