The implication of the Fourth Industrial Revolution on flexo platemaking
Historians point out the First Industrial Revolution as the shift from our reliance on animals, human effort and biomass as primary sources of energy to the use of fossil fuels and the mechanical power this enabled. The Second Industrial Revolution brought major breakthroughs, witnessing the expansion of electricity, petroleum, steel and new forms of power generation. The Third Industrial Revolution was propelled by the rise of digital systems, increasing connectivity and rapid advances in compu
27 Feb 2017 | By PrintWeek India
A continuous fight for survival
The concept of value continues to dominate conversations in the flexo platemaking industry. In response to this, manufactures of consumables and processing equipment are developing innovative value-based solutions to help flexographers take the right decision.
Right now, the focus of many farsighted flexo platemaking companies, whether they are trade shops or converters, is to stay lean and gain new business opportunities, by employing new technologies that requires less skilled personnel while offering greater capabilities to drive buyer engagement (higher quality), and faster response times.
Due to the nature of ‘modern’ flexo platemaking, we are now at a phase where being able to measure quality, cost and therefore, value, is a true challenge. Being able to talk about it is a feat in itself, as there are several objective barriers to that.
Flexographers are operating in a market where their customers, as well as the customers of their customers, don’t necessarily perceive or measure quality or value the same way. The different parties operating in the market are often constrained by their own transactional customers or other barriers that prevent them from making decisions uniquely based on quality and value.
Flexographers are facing increasing pressure to stay ahead of competitors old and new, with many established companies as committed to quality and value as any start-up.
The speed of change
Modernisation is the answer in a market where continuous innovation is the new normal, and the pace of change continues to accelerate.
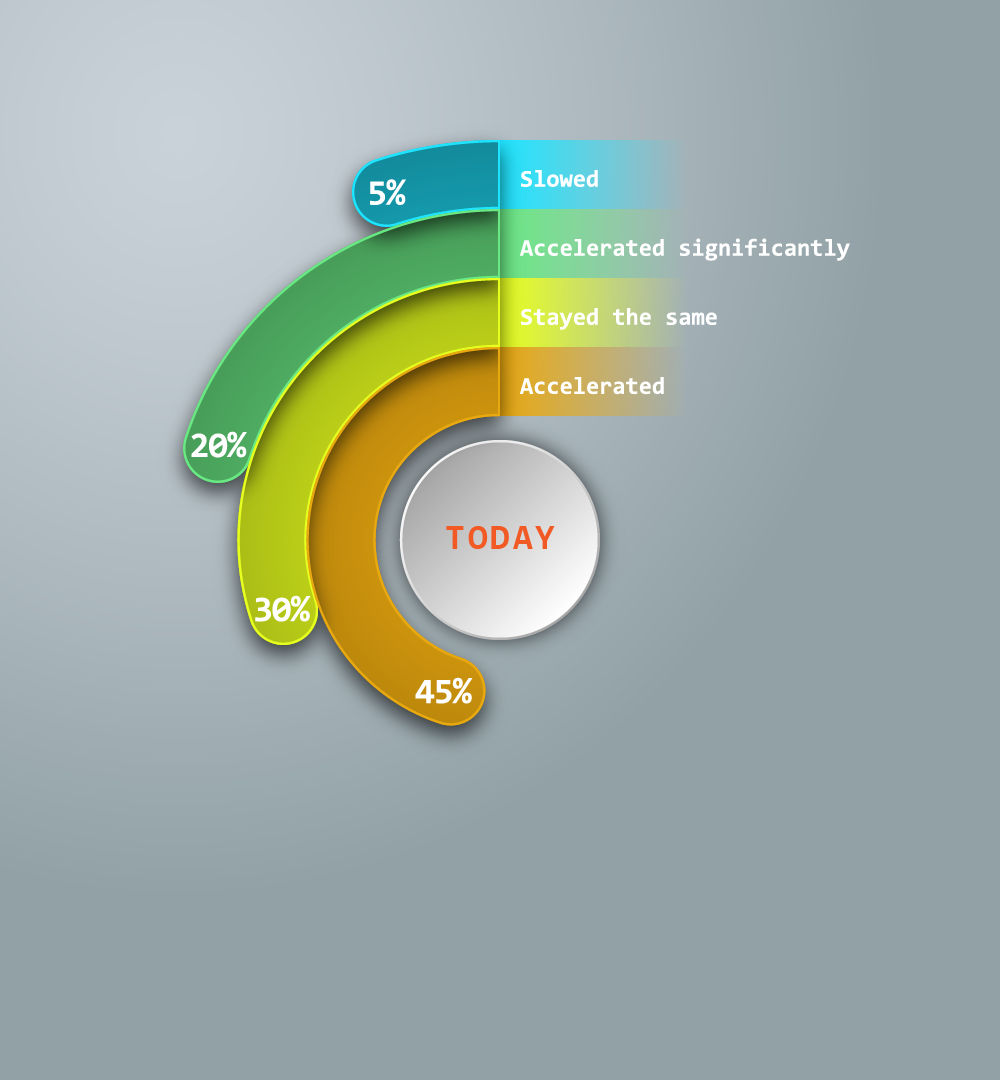
Faster time to market is a competitive necessity, and this pressure isn’t slowing down any time soon.
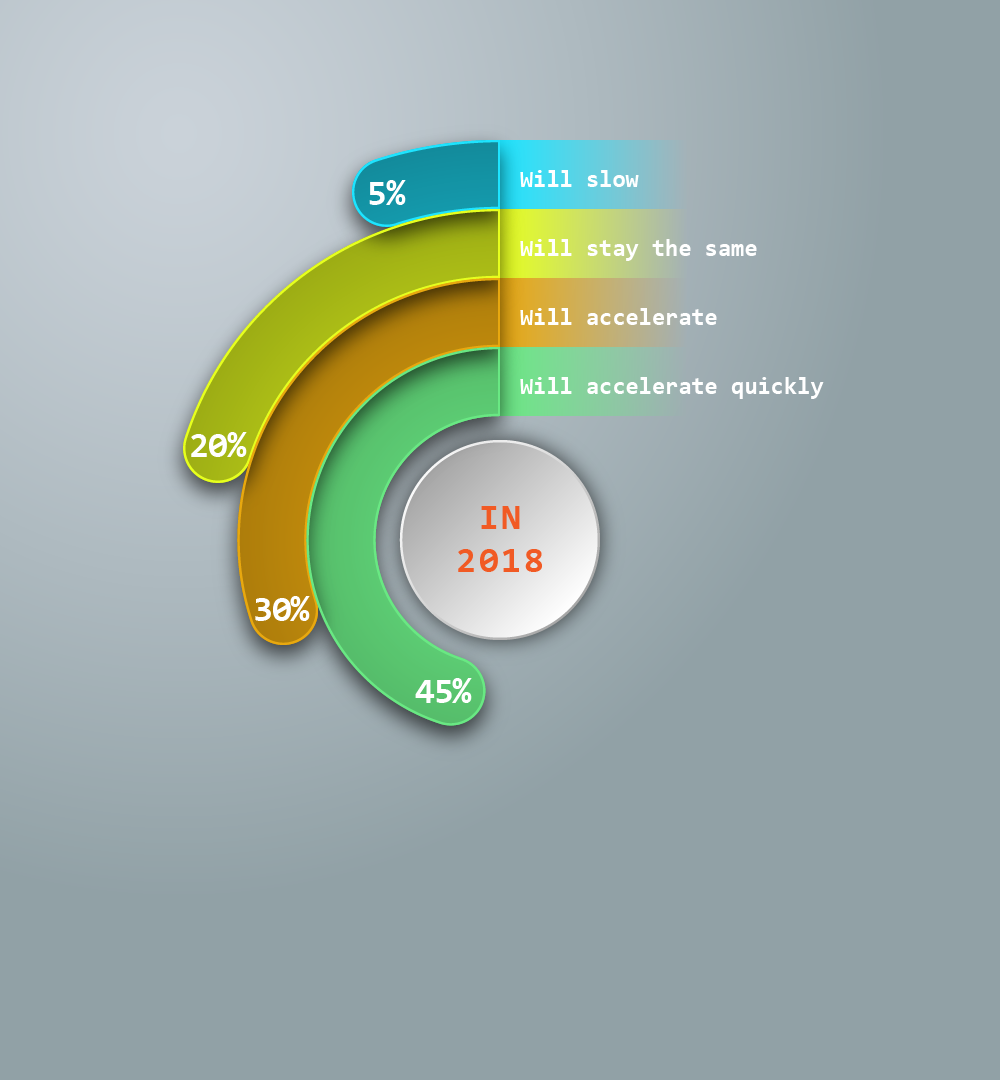
Our research revealed that flexographers with higher profit margins (high performers) are more likely to understand the speed imperative. These companies report feeling more pressure than their peers in a number of areas, including keeping up with established competitors, reinventing their offering (products and services) more quickly, and capitalising rapidly on new assets and new ideas.
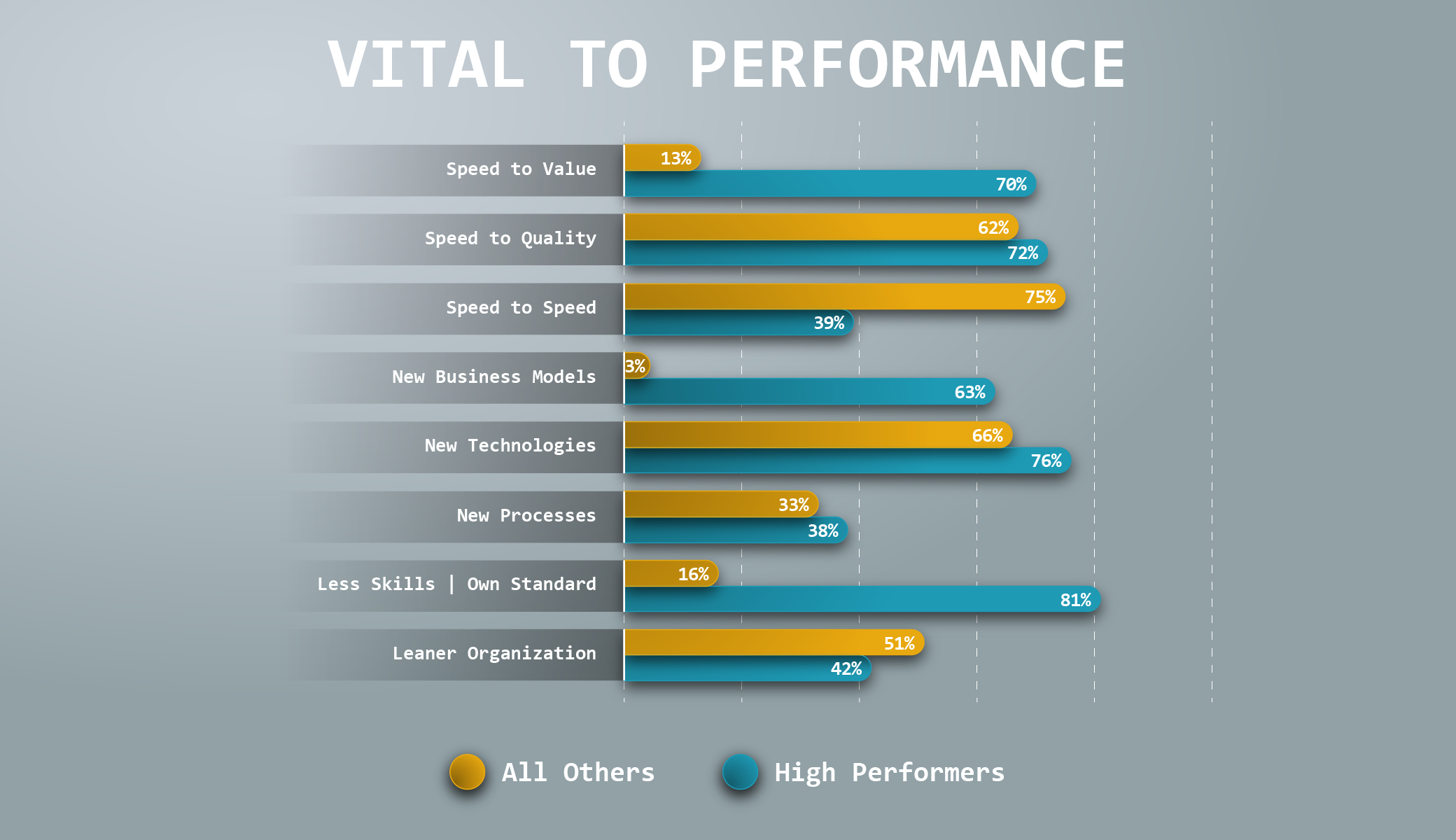
High performing flexographers are prioritising new technologies and a ‘personal’ plate processing standard and quality level that are less and less dependent on the skills of the individuals. Often they have built a solid toolkit to manage rapid change, internal and external.
The pressure comes from every direction, but flexographers are more concerned with threats posed by established competitors than they are with start-ups, although there is some variation by region.
While most flexographers are optimistic about their progress, with almost half of them say they will have accelerated their speed to value and quality in two years, they must bear in mind that their competitors may be making similar advances at the same time.
Evidence shows that the start-up mentality is not just for start-ups. The ‘old’ companies (those that have been in business for more than 10 years) are adjusting their assets, organisational structure and processes, to become nimbler, and are developing initiatives aimed at turning ideas into value and enhanced quality quickly.
Striking a balance
There is no easy answer or quick fix to the question of balancing value, quality and even speed. That is because every company has their own ambitions, priorities and thresholds; what is perceived as a good compromise to one, may feel untenable or even unacceptable to another.
Having said that we all know if we keep doing the same things, we generally get the same results. Similarly, if we keep doing the same thing when there are speed imperatives, we will most likely suffer even worse results.
So the time has come when flexographers need to do something different and new to move their business forward. Leaving the status quo is not easy, as it means action, effort and carries risk. If that implies a large investment in new technology, the stakes are even higher because the playing field is now moving so quickly.
Prioritising investment in new technologies requires a solid understanding of the state of the technology, the features and capabilities of the innovation available and the real impact of such technology on the company and its performances.
Adopting at the tight time
The idea of adopting new technology is to improve performances and fuel growth, not to chase the hype or follow the trend for the sake of doing it. The timing of adoption is important and it could bring unexpected opportunities, but early adoption could be void or even counterproductive if a company is unable to optimise the value from it. Flexographers need to have the right adoption strategy at the precise time that gives them the longest lifetime value at an acceptable level of risk.
One factor to keep in mind is that as technology spreads widely, the economy of scale expands but its value will start to shrink. Flexographers need to remember that this is what impacts the sustainability of any new technology.
Automation the future of flexo
There is at least one flexo processing equipment manufacturer that understood the flexographers dilemma and started developing a family of units that can be combined, right away or over time, to build a complete and fully automated unit.
This design approach is made of single units that can be independently purchased and then combined. The modular system is characterized by “standard” functional equipment prepared with interfaces that can be joined together to build different automated systems. Besides reduction in cost and flexibility in design, modularity offers other benefits such as augmentation and exclusion.
Adding new solutions by merely plugging in a new module helps overcome fast increasing customer demands and make the manufacturing process more adaptive to change. Automation is, instead, the answer to speed and standardisation.
Modular design typically requires shorter learning time. Automation dramatically reduces the risk for human slip-ups while improving overall safety.
Taking the leap of faith
The pace of change in business is accelerating, and rapid ideation and innovation are required for success in the next phase of this industrial revolution. To stay ahead of the curve and turn opportunities into real business, flexographers must invest in the right infrastructure and commit to reshaping their company structure.
Speed to value and quality has become a strategic imperative, and most of the successful companies will be those that move fastest.
Successful flexographers who have paved the way may be willing to share their experience to help others (potentially competitors) avoid some of the pitfalls. Or perhaps not.
Embracing modularity and automation is an alternative way to quickly take your business forward and limit the risk. Flexographers that want to survive will need to keep up with change and they can do it step-by-step. If, on the other hand, they want to thrive, they will probably have to be amongst those that lead the change.
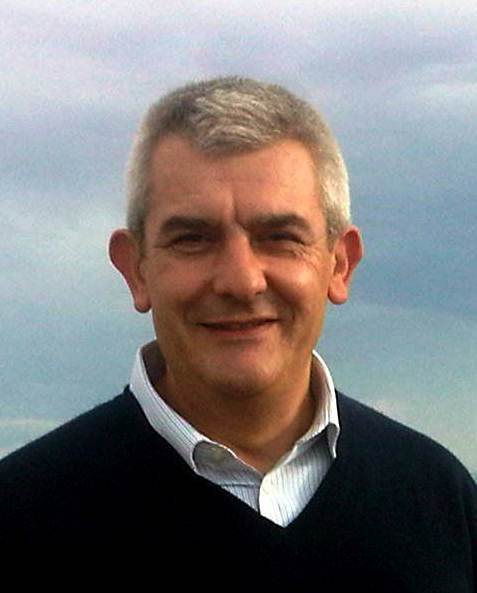
(Pier Luigi Sassanelli (SASS) is an experienced marketer with wide international experience in consolidated and emerging economies. Talented to identify business opportunities and translate them into profitable growth, he is currently a strategy advisor for several global and regional companies operating in food and packaging printing. Before, Sass was with DuPont for 30 years. You can find him in linkedin.com/in/sassanelli.)
(This is the first in a three-part series of articles on flexo pre-press written by Pier Luigi Sassanelli. Watch this space for the second and the third part of the series.)