At its open house in Japan in January, RMGT showcased three new technologies: the LED UV, tandem perfector and simultaneous plate changer. Rahul Kumar, who attended the event, provides the details
The Japanese sheetfed offset giant Ryobi MHI Graphic Technology (RMGT) organised a daylong open house in its manufacturing facility at Fukuyama, Japan on 19 January 2018 to showcase three of its offerings. The open house was attended by 96 guests from 13 countries, including India, Malaysia, Singapore, Thailand, China, Mexico, among others.
Among these, the first demo of the 10 series tandem perfector press (RMGT 1050TP-1+8+UV coating) showcased one pass both side printing for high-quality packaging printing at the speed of 16,200 sheets per hour. The second demo of 10 series (RMGT 1050 LX-6 + double coater) showcased 17,100 (optional) sheets per hour printing with inline quality control system (PQS-D). The third demo of 9 series (RMGT 920PF-8) LED UV printing press showcased A4x16-page convertible perfector with inline quality control system (PQS-D) at the speed of 13,000 sheets per hour.
While RMGT came into existence four years ago in January 2014, it was built on a strong technology backbone, thanks to the respective strengths of Ryobi and Mitsubishi Heavy Industries Printing & Packaging Machinery, a joint venture between which resulted in RMGT. Four years later, the demonstration at the open house signal’s RMGT focus on future innovations in the field of LED UV and packaging printing.
Today, RMGT is a 100-million Japanese Yen (JPY) capitalisation company with sales turnover of 28 billion JPY in 2017-18 manufactures more than 330 multi-colour printing presses per annum. India contributes to 4% of its business.
RMGT believes that LED-UV is the future, and being the inventor of the technology, it has advantages and better understanding of the technology. According to Vinay Kaushal, director, Provin Technos, the agency which represents the company in India, the RMGT solutions target three points – maximum productivity by minimised operators, people-friendly printing with easier operation and automated features and implementation of LED-UV technology.
During the open house, Katsushi Hirokawa, president, RMGT, confirmed: “We are committed to building relationships of trust not only with customers, but also with printing unions and associations, materials and peripheral device manufacturers, representatives and others who are involved in printing industry. Since our inception, we are working towards producing better printing presses to strengthen our customers so that they can produce their desired jobs.”
Hirokawa elaborated by adding that RMGT has developed its printing presses considering the global trends – extremely small-lot, various kinds of jobs and quick delivery; drop in printing margins; less experienced press operators and the increased cost of human resources, and concerns for better environment.
The strategy is already in works. As Kaushal confirmed, Provin Technos has sold more than 62 printing presses in India in the last three years. As most of these customers come from commercial and books printing backgrounds, he says, the company invited its customers to the open house to showcase the strength of its printing presses in terms of fast turnaround, multiple automatic features, from 0.2 to 1.2mm (G/micro flute) thick substrate printing, double-side printing in one go and compatibility of LED-UV technology. 12 printers from different parts of the country attended event.
If the idea was to inspire its existing customers to invest again, it definitely worked, as during the open house, Provin inked a deal for a RMGT 790 four-colour with coater printing press with one of its existing customers, Surat-based Shilp Art.
Advantage Japan
The production facility in Fukuyama (a 40-minute drive from the hotel) is on a hill terrain which can very well serve as an example of how to utilise such terrains in architecture. Surrounded by green, the facility has no boundary marker. The parking lot is at the back. While heavy machines, including CNC and others, were in operation inside the building, from outside, it’s hard to imagine it as a production facility. The building has been designed in such a way that all gases, fumes and other wastes were dumped inside.
The facility has two parts – ancillary equipment manufacturing and assembling unit. Each machine has a dedicated operator, and the person’s photograph is attached to the machine. According to RMGT, it gives sense of ownership to the operator and it is a helpful tool to increase his/her productivity.
Japan’s automated print firms
On the next day of arrival in Japan, the Indian contingent, along with this reporter (together with the delegation from Mexico, numbering 17 people), were taken to visit two commercial printing companies – Kumagai Printing and Sanshinsha. Both the companies are using LED UV technology on RMGT presses.
The Indian printers were suitably impressed. For one thing, the printing press was operated by a single person. Besides, the décor was quick futuristic, and innovative, including movable chairs on wheels in the boardroom. The entire production area was squeaky clean; the floor was so clean it looked like a mirror. The place was dusting equipment, the way an average building would have fire fighting equipment. The employees wore woollen gloves to avoid finger prints on paper. The paper handling was via forklift. Even extracting papers from bundles was systematic and impressive.
Both the printing facilities are equipped with liquid spraying to avoid electromagnetic field.
The Sanshinsha production facility is located near to the famous Tokyo Skytree – a broadcasting, restaurant and observation tower in Sumida. If you are nearby you can visit or you can take a photo.
The third plant visit was at Nishikawa Printing, a commercial printing plant two hour’s drive from Akihabara. The firm has three heatset web offset printing presses along with two RMGT presses. The heatset presses were operated by a single person and it was quite impressive.
The first demo
The first demo of the day was of one-pass both side printing for high-quality packaging on the 10 series RMGT tandem perfector press.
Simply put, printing presses are either straight (one side printing) or perfector (which can print on both sides in one go). Most perfector presses are conventional, the problem with which is that pages flip. As a result, printers need to keep gripper margins on both sides and grain directions of the paper also needs to be changed. Until 2003 or so, there was also a limitation on thickness of paper and printing speed on the conventional perfector.
Heatset web offset printing press was an option for high quality and long-run printing jobs at that time. It was feasible because jobs runs were long. Post-2003, run lengths started going down and heatset presses became unviable.
The next option was to do the job in two passes. Printers found conventional perfector suitable for normal books printing. High quality printing for packaging was an issue because of smudging gas printing inks do not dry immediately in sheetfed offset.
Then Mitsubishi came up with tandem perfector, where printing units are completely reversed. The advantage is that paper is not flipped and travels in one direction only. RMGT is the only manufacturer which manufactures tandem perfector in this design. The advantage of this design is that printing happens on one side in one go. Expansion is only on the same direction, so there is no chance of colour variation.
The new tandem perfectors are a perfect fit for high quality and long-run jobs. The design of the machine is enhanced by LED-UV by instant curing. All kind of configuration is available according to jobs requirement. The tandem perfector is for dedicated jobs and the applications are fixed on this machine. Since there is no reversal of paper, printing speed is maintained.
During the demo, RMGT showcased the capability of the technology in three machines, for speciality printing, for packaging printing and for publication and high-end commercial jobs.
However, it looks like, the Indian market will take time to upgrade to such a level, as in India, special fixed application jobs are not much. Top packaging printers do such jobs but the number is less. It is likely that the technology will come to India in the next couple of years and once the utilisation of the press reaches 60%, printers may opt for this technology.
If a printer requires five lakh of double sided printing and his machine capability is 30 lakh, then usability of the press is around 18%. Under the circumstances, investment in a tandem perfector doesn’t make sense, as a printer can print such kind of jobs with a multi-colour and a single-colour press in two passes. Once the requirement reaches 20 lakh or more sheets per month then the printer could opt for tandem perfector.
Blister packaging is the best example where both side packaging is compulsory, like toothpaste and other cosmetic products. Gillette, Duracell and others are best examples of that application. On top there is multi-colour printing and on back mono-printing containing information of the production. It can also be used to stop counterfeiting.
The other segment for tandem is high-end commercial printing.
Mitsubishi had a blanket-to-blanket printing press way back in 1985. It was single colour press and used to print on both sides. There was no demand of such kind of machines nowadays but every publisher has one or two such machines (pre-owned), it keeps printing small runs.
The second demo
In the second demo, RMGT showcased the standard packaging press with PQS-D system. This should 100% benefit Indian printers, where densities are measured in close loop without any manual intervention. It automatically takes the measurement after printing of every 30 sheets and auto adjusts the variables according to given parameters. It automatically scans the full sheet during the operation. No manual intervention is required. Thus, the consistency is far superior. Once a printer achieves densities, the printing press maintains it.
This is achieved with a combination of software and hardware. The hardware measures the corrections and software adjusts them accordingly. A mounted camera on the press finds the faults. The system is machine-specific.
If the technology finds a dot of 0.5x0.5mm, it will show the printed sheet as defective. The technology is especially suitable for pharma packaging.
Speed is not a problem. Mitsubishi launched a 16,000-sheet/hour machine in 2000. In 2007, Mitsubishi came with the V series. Then the company focused on productivity enhancement features and waste reduction features. Around 80 features were introduced.
The third demo
The third demo during the open house, the RMGT 920 with convertible perfector, was for books and publication printers. It is an eight-colour perfector press and showcased how it can help a printer by producing eight-up A4 jobs in 20x36-inches compared to 28x40 printing presses. The press can print 16-up in one go.
LED-UV makes it more beneficial. A printer can do high-quality commercial jobs on it because of instant drying. On a conventional perfector earlier, it was not possible to mount drying unit in between the press. If someone really wanted to do it then he had to put cylinder expansion which made the press really expensive.
It looks like the India market will adopt this technology fast. New Delhi-based Sanjay Printer has already installed such a press. It is a straight four-colour/2x2 straight perfector.
Indian printers at the open house
G Venugopal, Sterling Print House, Kochi
The open house cleared my doubts about LED-UV technology. The demonstration of LED-UV printing presses showcased ample amount of possibilities. I am impressed that I am going to finalise a 25x36-inch five or six-colour printing press with an online coater. RMGT showcased a different type of perfector in tandem perfector. But you need huge volumes to feed such a press. I could see availability of such kind of printing presses. One of the big takeaways was the instant drying of printing inks with LED UV technology.
We do packaging printing, but it’s not full-fledged. That’s why I am not going for 28x40-inches press. We shift between packaging and commercial according to market demands.
Attending an open house is a better idea than attending an exhibition because the entire manufacturing team is available for you with an entire range for machines and solutions. Exhibitions and other forums have limited time and access to the manufacturer.
BK Manjunath, Global Printing & Packaging, Bengaluru
I was impressed with the use of LED and conventional UV in the same press. Simultaneously plate changer and tandem perfector were impressive and useful technologies for a packaging printer like us. We have few products where tandem perfector is useful. It has a few constraints as well. Protective coating after printing is a must and there is no provision of coating in tandem perfector press; it is a requirement. If we consider coating in the printing press, then tandem perfector’s purpose is fulfilled. It is my suggestion to RMGT that they have to have online coating provision on tandem perfector press.
Blister packs are one of the great applications for tandem perfector press where you need printing on either side and coating on either side.
I fully appreciate the culture and ethics of the Japanese company. I was amazed to see that the people I met 15 years ago are still in the same company. This long association between employees and employer shows that people are loyal to the company and employer also takes cares his employees.
Vimal Sekhani, Nemlaxmi Books, Surat
The requirement of printing press or any capital equipment is an individual affair. It all depends that what you want to print or manufacture. We are in stationery manufacturing and 95% of our production goes into overseas market.
Tandem perfector is a suitable technology for the export market because jobs are long-run. Tandem perfector has to walk a long way for Indian market because of absence of long-run jobs and tandem perfector press does not have any space for coating and most of the printed jobs in Indian market demands coating. It is ideal for packaging printing.
LED-UV is a good technology and it does not require coating at all. But my concern is it could not spread in India well and printing inks are expensive compared to conventional inks.
I must admit that RMGT and its Indian representative Provin Technos are humble, polite and always ready to listen to their customers. Their behaviour before and after sales is the same. I always get services within 24 hours.
Manoj Nanavati, Shilp Art, Surat
The visit to the three printing presses during the open house was an eye-opener, especially in terms of printing press operation. I witnessed how a single person in Japan can run the entire printing press instead of four people in India, as the presses are fully automatised. It being a price sensitive market, it is tough to get ROI on fully automatic printing press in India, as more automatic features mean more investment. We also do not have long-run jobs in India as well.
We have LED-UV printing presses in India and few printers have retrofit LED UV on their existing presses. Indian printers have heard of LED-UV but very few are aware of its benefits. Tandem perfector was a new thing for me but unavailability of long run job is a hurdle in opting for the technology. Big packaging printers may opt for the technology when they have such kind of jobs but in a city like Surat, it seems tough. In our geography, every job needs coating and which is not possible on tandem perfector.
Asgar Husenibhai Sanchawala, Progressive Printing Press, Surat
We have seen three technologies, including LED-UV, tandem perfector and simultaneously plate changer during the open house and all were impressive.
LED-UV will definitely help packaging printers to grow in the coming years but the cost of printing inks and varnish is a big concern. In Japan, around 90% printing companies are using it. On the plus side, it has multiple benefits, including lower consumption of power and positive results towards environment. I can say that it will be a tool for fast and quality production for packaging printers.
Tandem perfector is an excellent technology for packaging printers who have long-run jobs, unfortunately which is not available in India for the moment. As long-run jobs (few lakh impressions of a single job) hit the Indian market, the technology will pick up. We must learn from work culture and ethics of Japanese printing companies, such as a single person running the entire printing press.
RMGT 9 series is suitable in terms of size, energy and printing plate consumption
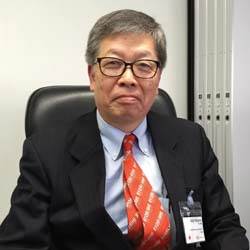
Rahul Kumar talks to Keiji Katayama, senior vice-president, (member of the Board), RMGT
Rahul Kumar (RK): Why are your machines so popular in India? Which were the most popular models in 2017 and why?
Keiji Katayama (KK): Earlier, most commercial printers used to print on 40-inch press but now they are using 36/37-inch press. They are reducing on size because 36/37 is good enough for A4 format jobs. On the basis of my conversations with commercial printers,I can say that most of their jobs are done with 36/37-inches printing. They do get jobs for 40-inch printing but its few.
That’s why our 9 series (920) is in demand. It is a suitable in terms of size, energy consumption, printing plate consumption and it is more economical on all the aspects. Printing is becoming too competitive. Our offering of this size helps commercial printers produce quality and quantity production within stiff competition. That’s why 36/37-inches printing press is becoming more and more popular in India.
We are building a range of offset printing presses. We call it 11/10/9/8/7/6/5/4/3 series. We manufacture 40-inch and bigger size printing presses, probably 70 sets per year. We manufacture 170 machines of 29x36/37-inch and 100 presses of A3 size.
In total, we manufacture around 330 printing presses per year. We could manufacture such numbers thanks to the joint venture between Ryobi and Mitsubishi.
RK: How has been the last 12 months for RMGT? Please share one high, one low and one wow moment.
KK: The high was when we could convince the US government publishing department to opt for RMGT 4x4 perfector nine-colour LED-UV printing press. They were using German 28x40-inch conventional printing presses, which had a lot of issues. It was a critical moment for us and everyone was very excited for it.
On the low side, I do not remember, but whenever a customer approaches us and we cannot deliver the machine within his demanded time frame, we feel bad.
On the wow side, LED-UV is becoming popular, but it is limited to commercial and books segment. No serious packaging printer has applied LED-UV technology yet. We found one big packaging printer who wanted to work with us. We set up a team who tested LED-UV for packaging printing applications. We alongwith lamp manufacturers, dyer suppliers, LED printing inks and coatings suppliers came together and tested it. It looked like that we have a future. It was a wow moment for us. We found that we could do it. Packaging printers do need LED-UV technology.
RK: There is a buzz in the market about LED-UV. However, do you think cost may be a deterrent why printers are not embracing it?
KK: LED-UV printing ink is expensive. But the fact is the mileage of LED -UV ink is higher than oil-based inks. Printers say LED-UV ink is double or thrice the cost compared to conventional inks. Our experience indicates that the mileage of LED UV/ UV printing inks is more than 20% of conventional printing inks.
LED-UV printing ink is not twice/thrice expensive compared to conventional printing inks. It is only 50% expensive. This should not matter at all, as LED-UV printing ink is just 8% of total print production cost. But look at the mileage and runability of LED-UV inks. It needs a big mindset change.
RK: What has been the impact of GST and demonetisation on your business?
KK: Some of our customers suffered because of it and it impacted us too. If anything new is introduced,it is a process and everyone has to go through the process. After six months of implementation of GST, everything is becoming normal and printers are becoming familiar with the process. The business is getting normal.
RK: Your Indian business contributes only 4% to your global business…
KK: This 4% is not in terms of number of installed machines, but it indicates monetary value of the business. I do not think Japanese, European and American markets are going to grow. The Indian market has a lot of potential along with the African countries. So we continue to work with Indian printers with our best solutions.
RK: RMGT became one of the most popular brands in India in the last few years…
KK: Our Indian partner is doing well. Their knowledge of the market and technical knowhow is a fantastic combination. It’s their commitment and support to Indian printers that helped us to reach to this level in such a short time.
RK: Your methodology to communicate the core values of the organisation?
KK: There is a huge difference in Japan and other countries. When we formed RMGT after the joint venture, the critical part of the operation was to bring people together from different cultures of working – Ryobi and Mitsubishi, as the histories of the organisations were different, technologies were different, and products were different. Basically we did not do anything special. People respect each other. It was a fundamental part of the company. Both the companies respect people.
Rahul Kumar's Japan Impressions
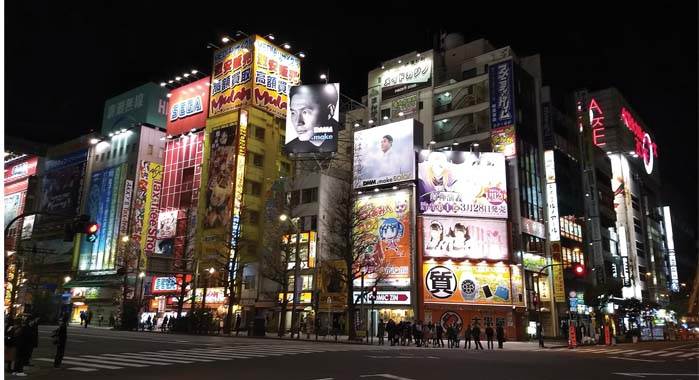
The five-day journey to Japan started on reaching Tokyo, a city of glass high-rises. And the people are polite and helpful. They may not know the language, but all of them have translator apps on their mobile.
In Japan, everything comes in miniatures, including the hotel rooms, but they were equipped with all facilities a traveller might require, including a massage chair and a night shirt. In the hotel, the breakfast table was full of natural and high protein foods, all packed and labelled, including the boiled egg. Now you know why Japan is the world’s biggest consumer in packaging. But there was no water bottle in hotels, because the tap water is potable.
There were few other things I found admirable.
Every shop has plastic bags at the entrance to put wet umbrellas to avoid rain water in the shop. The book shops are huge in terms of books and also have ample space to sit and read the books before buying; every seat contains an empty polythene bag to put trash.