Technical Article: The quality of your print begins before you print!
Many screen-printers, when they find bad printed texts or images in their production, have a tendency to think that they made some mistakes while printing.
05 May 2017 | By PrintWeek India
They suppose it comes from the ink, or the squeegee, or the pressure, or the speed of printing, their machine or their own incompetence to achieve a good print when pulling the squeegee by hand.
And this, whatever can be the application of the kind of screen printing they are doing in graphic, textile of industrial fields.
As matter of fact, you must never forget that success in screen printing is a whole where each of the needed operations have their role to play.
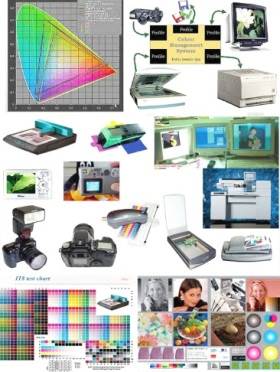
You can be the best printer in the world with the best machine, if the screen you use is bad, you have no one chance to succeed! And the screen can be bad for a lot of reasons, wrong choice of fabric, meshes opening or thread diameter, tension, ghost images on the fabric, unsuitable stencilling (bad source of light, wrong exposure time, quality of emulsion and its coating, vacuum frame damaged, insufficient depression for a good contact, wrong washing of the image, poor drying of the screen, etc.).
It can begin before the screen-making : bad film opacity, lack of resolution, lack of edge definition…
It can begin « before » the film making, on your computer: wrong files, insufficient number of dpi, lack of chromatic correction in process printing, design errors, poor image quality, problems with the fonts, etc.
Even the environmental problems can cause troubles: too warm air, too humid… or too dry. This means that you must have a very good control of the quality of your whole workflow, and this begins with:
Quality control of pre-press - films and screens
Creation of the digital basic files
In the current technology, the screen-printing prepress is now mostly digital. Despite of this, in numerous countries and in numerous small companies, the making of the films we need to obtain good screens remains often still analogue, and even “hand made”.
For the screen printers working this way, the end user or his local correspondent or agency often supplies films. Their problem begins so farther. (Cf. doing the films)
In digital, files are most often created by the customer, his studio or his agency or even by the printer if he is equipped, the digital file is the base of the supplied image, texts, artwork, etc.
What characteristics should present the films or these files according to the various possible applications?
• line artwork (resolution - definition)
• four colour process
• indexed colours
• additive special effects
Line screen printing
Tools for control:
Good magnifiers 10 times, or more (50 and 100 times), the computer with its monitor and the needed software.
The original can be a hand drawing, in one or several colours, and can be scanned with a good flat scanner or a digital camera with high resolution. Drawing in China ink, the inactinic films cut manually or digitally, or even films directly generated (take care of the quality) through digital ink jet printing on thin special polyester films.
The scanned file being mostly produced in PDF, Photoshop – TIFF - I advise to convert it in Illustrator vectorised, either directly imported under Illustrator, to have a better quality of curves (in Bezier).
Naturally, one can also create directly in digital under Photoshop, Illustrator, CorellDraw, Indesign. If for some reason, the line drawing is not vectorised, take good care of the resolution under Photoshop: control the quality of curves on the film magnifying 10 times of more, or also on the screen of the monitor in wide enlargement strong swelling if you can reach the basic file: no stairs. I advise a resolution of 1.200 dpi or even 2,400 dpi, in TIFF or EPS of course.
Please , control also the “blackening” on the file: he should be 100% of black (in levels of grey) And 100% also in CMY, besides the black, in CMYK. Take good care also of the quality of white in the background (0% in each basic colours CMYK).
If there are two juxtaposed colours (or more) and if you judge that you need a slight overlapping of a film on an other one – for register safety - make it only between 0,1 and 1 point maximum.
(This is the first series of articles on screen printing written by Michel Caza. Watch this space for the next part of the series.)
About the author
Michel Caza is a multiple award-winning leading light in the global screen printing industry, and one of the ‘founding fathers’ of Fespa in 1962 and has been a Board Member since 1990.
As a pioneer of fine art screenprinting, Caza has collaborated with many world-famous 20th Century artists, including Dali, Lichtenstein, Matisse, Miro and Warhol, as well as numerous illustrators, studios and comic designers.
Caza is a great supporter of DMI in Vasai since its inception and his technical articles are published in Grafica News India.