Product Watch - Tec4Check MediaCheck
With efficiency benefits and the power to woo and win customers, there’s a lot more to this print inspection software as the 20 locations that use it, prove to Rushikesh Aravkar.
28 Oct 2016 | By Rushikesh Aravkar
W hen Mumbai-based supplier Advanced Graphic Systems (AGS) added German print inspection software Tech4Check to its kitty early 2016, it experienced an upturn in demand from the pharma converters.
“When AGS came in there were already 10 locations running Tec4Check in India. In the last seven months, we have doubled this tally and two more installations are in progress as we speak,” said, Vishnuu Kamat, vice-president – sales, AGS.
One of the reason he believes that pharma converters are spending on print inspection software is because they realise they can’t afford to deliver inaccurate packaging, labelling or patient information leaflets (PILs), when the pharmaceutical companies pay a great deal of attention to ensuring they’re compliant with good manufacturing practices (GMPs) and US Food and Drug Administration (FDA) regulations when manufacturing a drug.
According to industry experts packaging problems due to incorrect information on packaging could result in recalls, and increased efforts in rectification; a single recall can cost easily up to USD five million in revenue.
Another reason that converters are spending on such software while tightening their belts in other areas is because it has become a must-have for companies competing for business with biggies and brand owners. It can be observed that a lot of software licences are bought as a way of winning or retaining customers, it just provides an edge.
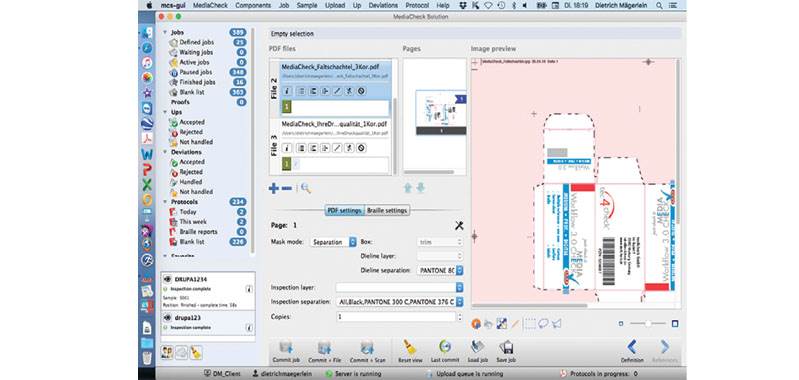
Tec4Check’s clientele is impressive. Temple Packaging with four locations running Tec4Check, Award Packaging at Mahape and Silvassa, Kalapi Offset, Mayura Offset, Budhraja Packaging, Printmann, Rich Print and Rich Offset and pharma companies like Mylan and FDC among others.
Differing approaches
Today, when a customer-approved artwork is opened by a pre-press operator, Kamat says, a lot of issues can occur then and there without the operator realising. “This can be errors due to software version mismatch, font missing or font replacement, mirroring of images etc. Some print firms add barcodes, up numbers, logos etc on the customer-approved artwork and while doing that the operator unknowingly deletes something.”
Most of the pharma packaging converters today deploy some sort of manual print inspection. But approaches vary widely and inefficiency seeps in. “The common method used widely is to print the customer approved PDF on butter paper and superimpose it on the printed output and then manually verify the correctness,” says Kamat stressing the need for automation in the otherwise manual process of proof checking the artworks at the pre-press end. “This still works if the text is in English. When it comes to an unfamiliar language such as German, French, Russian or Indian languages like Tamil, Gujarati etc, it is practically impossible for the pre-press operator to locate an error.”
Tec4Check works in two modules: one module operates before platemaking process where it compares customer-approved artwork with single-up or multi-up PDF that will be used for platemaking; in the second module it compares the customer-approved artwork with the scanned printed sheet.
“Using a pixel-to-pixel comparison between PDF files or between PDF file and printed sheet scan, the software displays only the relevant deviations and lets the user decide which of these deviations are true errors. Such software-enabled comparative checking makes sense at many stations during the production of PDF,” adds Kamat.
This verification is independent of the language, the font and the kind of content. It does not matter if the data in the PDF file is a raster image or vector or text. The resulting visual appearance of everything: text, images, line-art is compared to find deviations in the text of any language and font, in codes of any kind, in drawings or in images.
AGS supplies a 36-inch Graphtec scanner that has been tweaked to handle paper as low as 29gsm so that even PILs can be handled. Scanning the first saleable sheet and comparing it with the customer-approved PDF is crucial. Kamat explains, “If there is any error in the print set-up, such as the wrong plates being used, it will go unnoticed unless the operator spots it.” The Tec4Check loads the signed-off PDF and uses this to check the first scanned sheet, so it does not rely on the operator’s observation.”
If there’s a heavy colour in the artwork, the pixel density in the area will be high, so in the case of shade variation, there will be lesser number of pixels and the software will identify a deviation, now it is up to the operator to accept it or reject the deviation as an error. Therefore, running the software is the easy part, as Kamat says, the effectiveness of the software lies in how the operator analyses the deviations detected by the software and then takes corrective action.
Stand-out features
The efficiency of such proof checking software is put to test while inspecting a lock-bottom carton job. “What Tec4Check does best is it has the capability to accept multiple reference artworks. So when you impose a lock bottom carton on a sheet you can input two references one for each carton in the lock bottom pair and provide the number of ups for the two. The software automatically determines which up to be compared to which reference,” simplifies Kamat.
Such a feature comes handy especially while ganging multiple jobs on one sheet. “Five different jobs on one sheet can be easily checked with five different references,” says Kamat.
Another stand-out feature probably unique to Tec4Check is of rectifying repeated errors in one go. “If you click on the first up and the software highlights an error and if that error is being repeated in the other ups, there is an option which says ‘show related’, wherein you can group all the similar errors and make a decision in one go,” says Kamat.
The Tec4Check can be installed as standalone software on a local computer or it can be set up as server-client architecture. Kamat prefers a client-server architecture to be an efficient choice for the users. What it brings to the table is, a flexible integration into existing workflows to rapidly respond to optimise work processes. It also enables the department head to monitor the jobs at different locations, if that is the case. “Almost every installation of Tec4Check has been a server-client system. That is because the print firms who opt for Tec4Check also understand the effectiveness of client-server architecture,” says Kamat.
“Every action and communication with the server is logged including the user and client and can be found in the report. The detailed report of accepted and rejected changes can also be generated and submitted to the customer as a quality control measure.”
To sum it up, with Tec4Check quality control happens at the point where deviations occur. Thus, time, as well as costs, can be saved and the chance of human errors is eliminated. Plus all this can be demonstrated to your customer and document for them.
With so much of a brand’s reputation resting on the information on-pack, brand owners can’t afford to have mistakes creeping in – and, therefore, neither can packaging converters.
Contact
Advanced Graphic Systems
Vishnuu Kamat
+9122 67812000
vishnuurkamat@agsindia.com