Where is print poised in the Drupa year? - The Noel D'Cunha Sunday Column
In this Sunday Column, CG Ramakrishnan discusses the transformation of TechNova; and how the company that was born three decades ago, is embarking on a green mission, to providing digital solutions
12 Aug 2016 | By Noel D'Cunha
Noel D’Cunha (NMD): Drupa? A reasonable success for print?
CG Ramakrishnan (CGR): Drupa 2016 not only provided a lot of opportunities to generate business but also to update one’s knowledge about the latest trends and technologies in printing.
NMD: How has the Drupa year been for TechNova?
CGR: TechNova had a large deputation to Drupa 2016 with clear objectives. Our team visited Drupa 2016 achieved most of them quite satisfactorily. One of the critical objectives was to assist our Indian customers identify and evaluate technologies, systems and consumables on offer at Drupa 2016, with the help of our alliance partners.
NMD: Any business deals concluded?
CGR: We were able to help many of our customers conclude deals, and have initiated many more that would fructify soon. Our customers have given a resounding yes to TechNova’s transformational strategies and made sure we have enough reasons to cheer.
NMD: TechNova has been at the forefront of inking new alliances? Be it: Konica Minolta and Duplo in the past or the recent one with Esko?
CGR: TechNova has always been at the forefront of innovating for our customers, be it by developing and manufacturing in-house or making the best-in-class solutions, products and services available to the Indian graphic arts industry through alliances. Today, customers are feeling the need to have a partner they can trust to help them make meaning of hybrid ecosystems, connecting offset and digital printing technologies.
NMD: What is the strategic rationale behind the slew of alliances?
CGR: It is by virtue of various domestic and global alliances that we have been able to introduce products like spray damp systems; a range of software for quality and productivity enhancement; high-speed low-energy automated CTP systems at entry level costs; inkjet CTP systems; and specialised services. All our alliances are formed with the singular purpose of making the best end-to-end solutions available for our commercial, publishing, packaging and newspaper printing customers and keeping them ahead of the curve. We are venturing where our customers want us to be in: green, digital and packaging.
NMD: Our estimate indicates the offset plate usage in India is 40 million sq/m. At the existing currency rates; this works out to a market size of USD 164- to USD 175-million.
CGR: India’s consumption story is still intact and as an essential consumable, plates will ride that growth. The usage of offset plates in India has continued to grow in the last few years albeit at varying growth rates. This is in contrast to other developed print markets globally, which have seen a sharp decline.
NMD: Are these healthy numbers?
CGR: Yes, while the top segment is fiercely embracing green plate technologies, conversion to digital plate technologies at the mid-bottom of the pyramid continues.
NMD: What have been the growth drivers?
CGR: The major growth drivers in India are: a green journey, sustained conversion to a digital plate workflow, India’s GDP growth trajectory, government’s drive for literacy and the continuous excellence of Indian printers.
NMD: The question on many lips: how does the print industry work to build print optimism?
CGR: This is something that we all need to work on. The Indian printing industry has many inherent strengths, such as: entrepreneurship in our DNA, a tech-savvy nextgen, IT and engineering talent, English speaking population, low-cost manpower, etc. We are blessed with a large domestic market being driven by stable political environment, robust economy, growing GDP, various literacy drives by the government, and a real opportunity to become a major hub for exports in book printing and packaging printing segments.
NMD: In what way can one boost the print climate in India in 2016-17?
CGR: To exploit these opportunities, we will need to overcome the challenges we face, which are both external and internal, by formulating well thought-through competitive strategies and practicing operational excellence in terms of technology, quality and cost management.
NMD: By the end of 2015, almost about 50% of Indian newspapers had opted for chemistry-free plates...
CGR: When TechNova introduced VioGreen plate in 2010, India became one of the only four countries in the world to have its own chem-free violet CTP plate. Within five years the Indian newspapers have converted 50% of their consumption to chem-free plates. This is primarily due to the major reduction in water and chemistry usage they experienced, without compromise in printing quality. This dovetails very well with the other sustainability initiatives of newspapers.
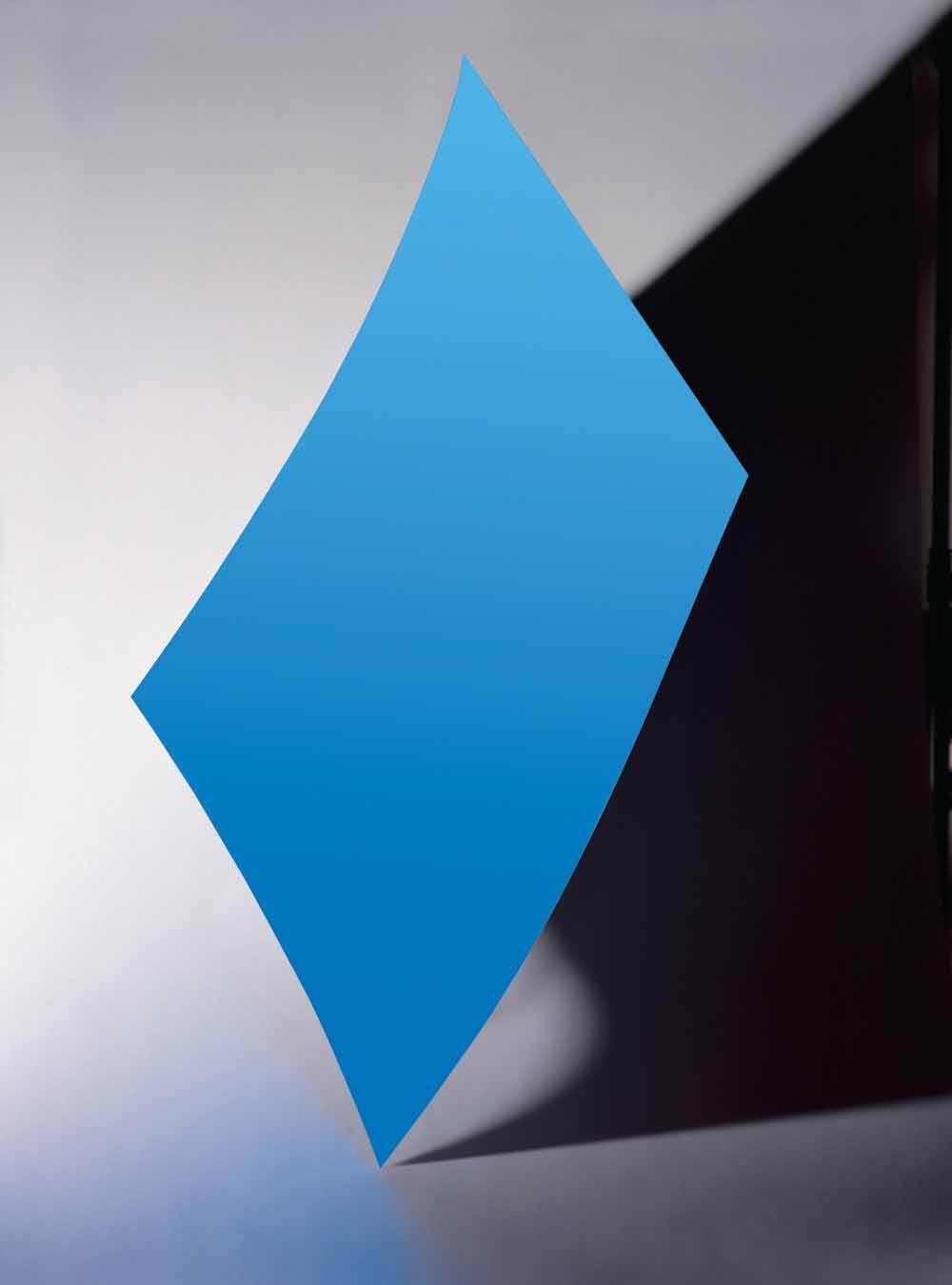
NMD: By when will this number be 100%?
CGR: Indian newspapers are embracing green plate technologies at a rapid pace. We are committed to fulfil this appetite faster and hope to convert the balance 50% in less than half the time it took to convert the first 50%.
NMD: Is this a part of TechNova’s Go Green strategy?
CGR: Yes, we are very proud to see that Indian newspapers are at the forefront of the green printing movement. We are privileged to be a partner in this journey.
NMD: What has been the trickle-down effect of Go Green among Indian newspaper plants?
CGR: Indian newspapers are embarking on multiple environmental projects even outside of printing, like water conservation, reduction in the disposal of harmful effluents, tree plantation drives, and are seeking the green gene in products other than just plates. TechNova supports the Go Green journey of Indian newspapers by supplying not only green plates but also a whole bouquet of green chemicals, water filtration units, low-energy CTP systems, etc. We are fully committed to innovate, develop and manufacture more and more green products for the graphic arts industry in general and Indian newspapers in particular.
NMD: TechNova introduced VioGreen, the chemistry-free violet CTP plates in 2010 for the newspaper industry. Today, the chemistry-free technology has been extended to cater to commercial as well as packaging segment. Your view.
CGR: Having witnessed substantial benefits and the excellent performance of VioGreen and VioGreen Plus plates in newspaper printing, commercial and packaging printers have also readily embraced our Green CTP plates. Today, TechNova is one of the very few companies in the world which offers the full range of green CTP plates.
NMD: What has been the success rate?
CGR: Customers are excited with these introductions and the conversion rate is very steep. We are more than happy to supply and support whichever technology our customers choose, based on the nature of job and process needs.
NMD: One of the silent success for TechNova has been the iCtP (Inkjet CTP) base in the Saurashtra region of Gujarat plus mofussil parts of India.
CGR: We have an installation base of 300+ SmartJet inkjet CTP solutions, predominantly in the newspaper and book printing segments. We continue to keep our successes silent. We measure our success by the level of satisfaction our customers express and the benefits they accrue from the solutions we provide and we believe that this is a constantly moving target. TechNova’s SmartJet inkjet CTP solution is currently using MetiJet metal inkjet plates, PoliJet polyester inkjet plates, and PosiJet clear inkjet films.
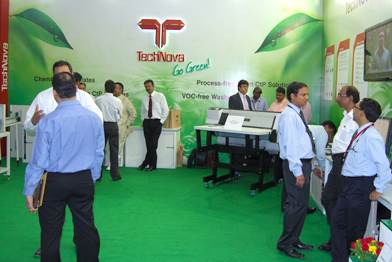
TechNova stall at Wan-Ifra
NMD: Has TechNova underplayed its hand with this no-process low-cost CTP system?
CGR: Rather than celebrating this success, our team is keenly focused on fine-tuning the GreenJet chem-free metal inkjet CTP plate, which will be imaged by the same system and can be taken to the press directly after imaging, eliminating the exposing, processing and developing stages. GreenJet will be a big value addition for our iCtP customers.
NMD: A lot of SME-size printers want to know where is the next big buck in print industry going to come from? What would you say to such printers?
CGR: It will continue to come from packaging. It will come from offline specialised varnishing, food-grade barrier coatings application, from specialised digital work like photo albums, art reproduction, etc. Print is transforming from “print of messages” to “print of things”. Seek every opportunity to innovate. Go Green, Go Digital, Go Packaging.
Chemistry-free vs processless plates? What's the difference?
Both are environment-friendly CTP plates. That’s where the similarity ends, everything else is different. The chem-free variety is available for both violet and thermal imaging technologies. However, the process-free variant is available only for thermal imaging technology.
And this is not so for chem-free?
After imaging, the chem-free plates need to be passed through a small foot-print clean-out unit for removing the non-image area with the help of a PH neutral gum. The process-free plates are directly mounted onto a press after imaging and the non-image area is removed on the press. To answer your question, both the variants have benefits and challenges which are unique to each.
What is TechNova’s offerings in this range?
TechNova offers a full range of green CTP plates, viz. VioGreen Plus, the chem-free violet CTP plate; Azura TU - the chem-free thermal CTP plate, and Azura TE - the process-free thermal CTP plate. We are technology neutral and are happy to hand-hold our customers to evaluate and select the best plate which is suitable for them. This is based on the customer’s business needs, nature of jobs and process parameters.
TechNova’s seven-step guide for printers to consider while making a choice between a chem-free plate and a process-less plate
1. Since the coating from the non-image area of a chem-free plate is removed in the platemaking stage itself, dot measurement and plate calibration is much easier as compared to the process-free plate.
2. In the process-free plate, mistakes if any, become evident only after the plate has been mounted on the press, leading to machine downtime.
3. Since removal and cleanout of the non-image area of a process-free plate are carried out on the press, it leads to precious machine time loss and high paper wastage during makeready.
4. The dampening solution and ink on the press could get contaminated with the removed coating from a process-free plate. With the chem-free plate, this is done in the platemaking stage itself.
5. Fingerprint sensitivity of process-free plates is very high. This may result in the non-image area, having fingerprints catching ink on the press leading to an increase in paper wastage and machine downtime.
6. Chem-free plates can work with standard press room chemicals whereas process-free plates require compatible pressroom chemistry to achieve optimum performance.
7. Since the chem-free plate is more robust, it is capable of giving higher run lengths as compared to a process-free plate.