Innovative investment in technology plus cost-saving measures play a key role in making Lokmat the largest read Marathi newspaper, finds out Priya Raju
Founded on 15 December, 1971, Lokmat Media is a multi platform media company with interests in a diversified portfolio of publishing, broadcast, digital, entertainment, community and sports verticals. With Karan Darda, executive director, at the helm of affairs at Lokmat Media, Lokmat is currently the largest read regional language Marathi newspaper in Maharashtra and Goa states.
The PrintWeek India team visited the newspaper production plant of Lokmat, in Sinhgad, Pune. The plant structure stands tall with its signature brick-red colour exterior, and is spread across 1.5 lakh sq/ft area. The plant currently prints 26 crore pages every month and consumes 1200 tonnes of paper.
Lokmat’s production units are spread across Maharashtra with twelve print production plants. With circulation of 18 lakh copies in Maharashtra and Goa, they have a major chunk of the market share. Lokmat also caters to the Marathi speaking population outside Maharashtra. It has editions in Indore (Madhya Pradesh) and Belgaum (Karnataka). On 21 April 2009, Lokmat launched its Goa edition (Marathi) primarily for the Marathi-speaking population of North and North-East Goa.
Lokmat is on a growth path, with all the up radation of its press unit as well as its pre-press with latest technologies. Despite tough competition from the existing Marathi dailies as well as new launches plus the digital media; the revenues of Lokmat have grown steadily.
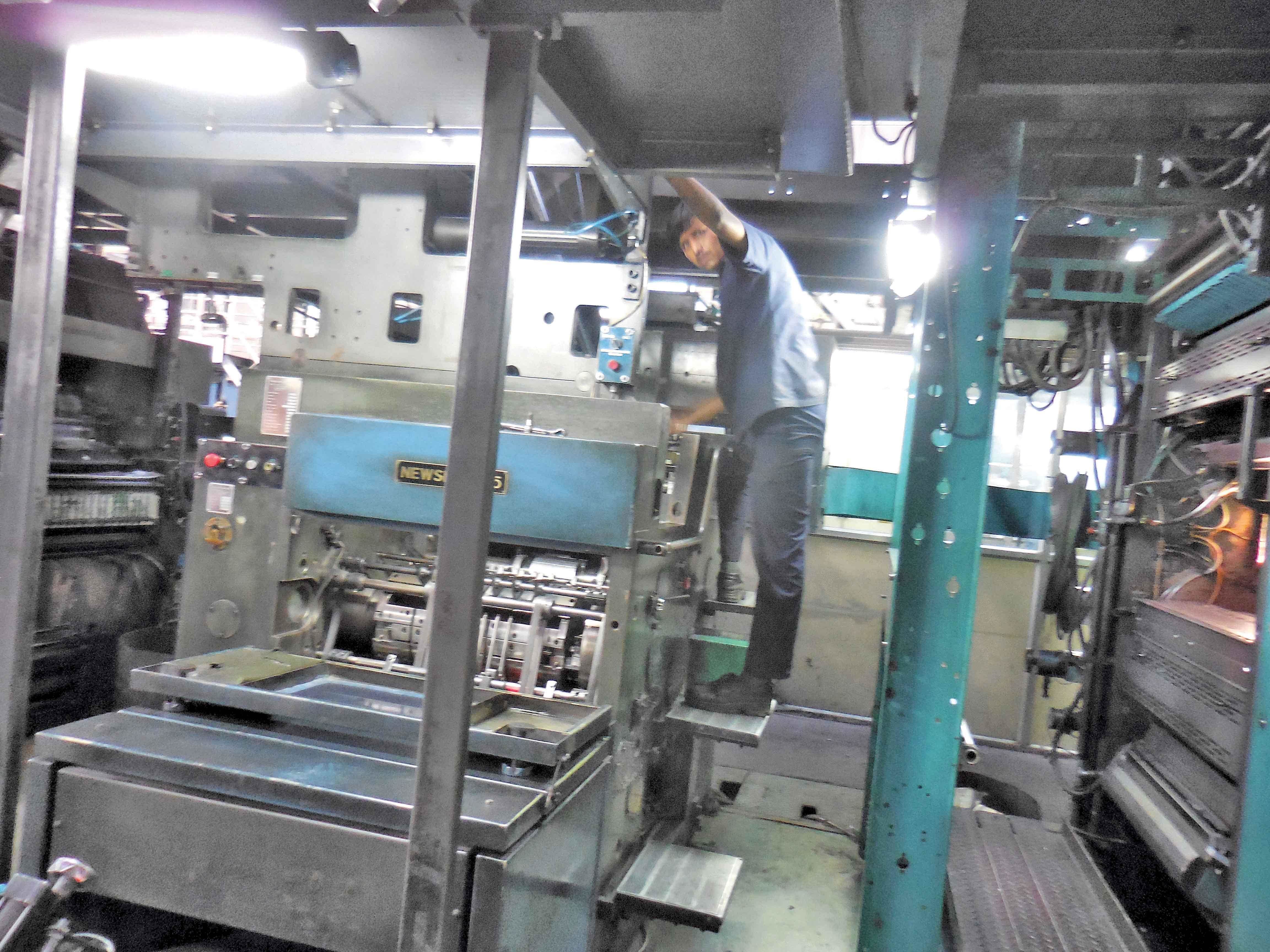
Behind the scene
The career of Neeraj Mahajan, the vice president – technical, Lokmat Media, spans over 25 year in the newspaper industry. Mahajan oversees the operations of all the twelve production sites across Maharashtra.
A mechanical engineer entered the newspaper industry after graduating in 1988. Prior to moving to Lokmat Pune, Mahajan was based in North. Mahajan has used his vast experience in the industry and spearheaded the new concept of 2C units in their production plants. It is under his supervision that initiation of the new concept of 2C system was implemented in Lokmat’s plants.
Novel concept
As a part of the plant expansion plan, 2C printing unit which acts as an add-on in existing Hiline Y printing units for 4x4 printing was mounted on the existing Manugraph Y units. The idea behind introducing this concept was to save cost, since a new tower would mean an investment in crores. Mahajan says, “This technology was implemented for one-fifth of the cost of a new tower and also; the existing press could be utilised.”
“All the initial inhibitions and problems arising were taken care by Manugraph and their team,” says Mahajan. Lokmat plans to invest in another five 2C units. The units are being commissioned in three locations. “Later, we also plan to upgrade the remaining units.” says Mahajan.
One of the advantages of the 2C unit is that all the operations from pre-press to post-press remain the same. “The number of colour pages required in the newspapers is going up and with a 2C unit we are able to print 4x4 colour inline,” explains Mahajan. “The unit has helped in reduction of web breaks and faster webbing up when compared to a tower,” he adds.
Inspection need
Turnaround time for newspaper printing is short. Thus making job printed right, the first time and on-schedule delivery is an imperative. Things were working fine, but Lokmat faced one peculiar problem with the 2C units. At different speed and at the time of pasting a huge variation in registration was seen. The problem was more acute at the winding system. Mahajan says, “Due to all the problems, at one point of time we thought that the system would not work with our press.”
At this point of time Iware came in with a solution and helped in integration of the units. Iware engineered the Intelligent Color Register Control Solution (ICRS) system. Iware colour registration system is built with a high-speed colour camera and achieves automated colour registration in web offset presses both during start-up and throughout the print run.
Mahajan says, “A customised solution and flexibility in payments favoured our decision towards the Iware’s embedded hardware and software. Also, the hardware and software solution is fairly simple and can also be fixed locally if issues arise. The next step is the training,” informs Mahajan. These systems are currently mounted on the Manugraph machines which are installed at the facility.
Commenting on the decision to invest in the system, Mahajan explains, “The solutions provided by similar software developers were expensive and neither concrete, nor customised to our requirements. The Iware software provided us with cost-effective solution and resulted in the reduction of wastage from 300-400 pages in a single system at the time of splicing on the 2C unit to almost zero. More importantly, the start-up waste has been reduced by 50% on the press line.”
The Iware system has now been installed across Lokmat’s three sites among 12 print production plants spread across Maharashtra. Two units have been installed at Kolhapur, three systems at Nagpur and four systems at the Pune plant.
Standardisation and technology
Lokmat’s press is standardised to ISO-39 for a dot gain of 26 as recommended by IFRA. The densities that they follow meet the IFRA LAB values.
Additionally, Lokmat has invested in colour management software from GMG at all its centres. “The benefits offered by the software and ROI has been at par, says Mahajan. “We are able to get predictable results, now.” Mahajan says. “Also, we have not had any kind of complaints from our advertisers in the last one year and the ink mileage has improved from14,000 to about 18,500.”
The two CTP units at Pune from Agfa churn out 45 plates per hour on the 8-up system. Mahajan plans to upgrade the system in future.
The future map
Lokmat has decided to invest and upgrade its machine. Lokmat has commissioned a new Orient press at its Nasik plant. Currently, the Orients’ press has been installed at Nagpur, Nasik, Solapur, Akola and Nanded. The cut-off maintained currently is 546mm, but soon they plan to standardise the cut-off to 533mm.
This will result in minimising the wastage and will save 40mm of paper. “Since, in newspaper industry, 60% cost of production is paper, this will help us save cost up to Rs 20 lakh,” says Mahajan. Talking about the non-print space, Mahajan says, “It is still in a nascent stage and efforts are on to develop the digital medium.” Lokmat has managed to control the total group waste at 5%.
Lokmat also believes in green initiatives and is one of the newspaper plants which has equipped itself with solar power in two of its plant. The Nagpur and Aurangabad plant is equipped with 0.33 MW power panels and runs the day time production for its supplements on solar power.
Specifications
|
Total printing plants: 12
|
Total pages printed (Monthly): 130 crore pages
|
Paper used (Monthly at Pune): 1200 tonnes
|
Circulation base (Maharashtra and Goa): 18 lakh
|