A PrintWeek India -BMPA forum to discuss printing issues including narrow web labels press and UVCTP technology, IR inks, and related topics in adhesives and paper.
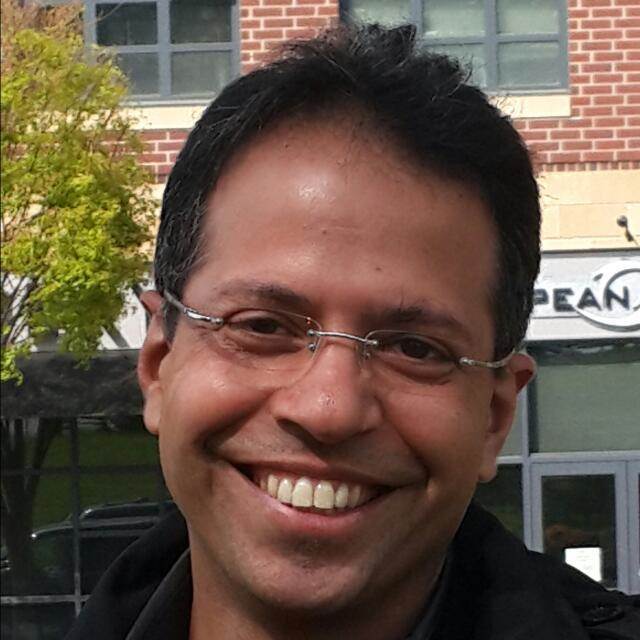
Recently we did a print run of 8000 books of 180 pages on 130gsm BILT matt paper. No online coating was done on the inner pages. In the past we used to find a lot of hand stains or marks on the first and last page leading to wastages and loss of time. This time we used matt online coating for the first and last page and we found a great reduction in the wastage. This results in the cutting of the blanket but is well worth it vis-a-vis the cleaning and the chance of falling short on quantities as a result of stains that cannot be removed.
Jehangir Surti of Prodon Enterprises: The matt coating actually blends quite well especially if the first and last pages do not have much print. I also recommend using dull matt varnish (from Actega) as visuals on art paper are hardly noticeable.
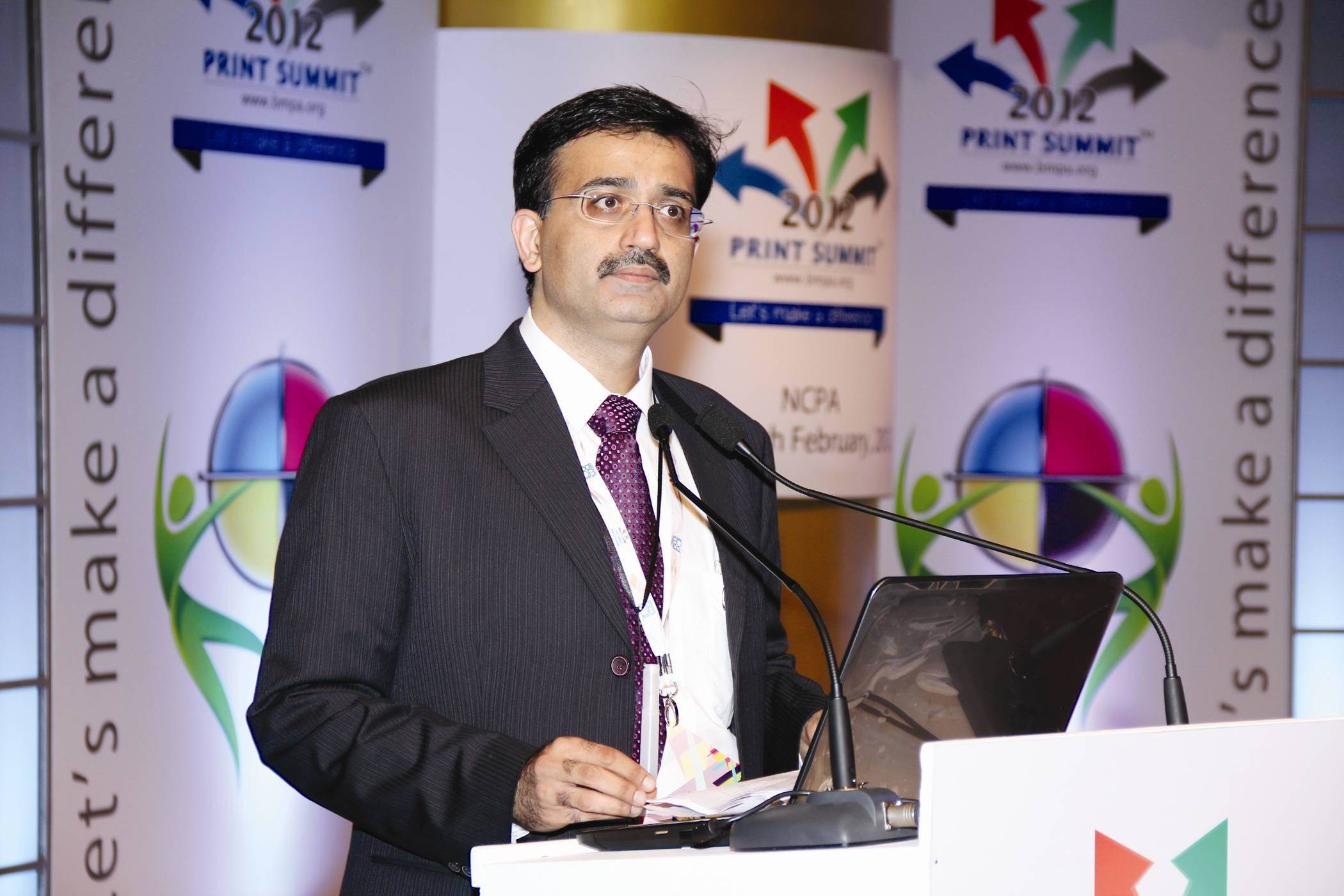
When it comes to sustainability in printing, we see only big printers taking initiatives and implementing them. So what according to you are the Jugaads that can be made on-press or on a press shop-floor to achieve optimum sustainability?
Faheem Agboatwala of Hi-Tech Printing Services: I believe sustainability is a hugely ignored subject in India only because there is nil or little answerability and fines. Once these get enforced then we will be forced to act. Currently several "green" initiatives are done only because it looks and sounds "cool".
Here are some simpler things any printer can follow - big or small.
1. Using soya-based inks over conventional inks
2. Switching to using process free plates thereby reducing VOC and water usage
3. Dissuade clients from using lamination (film coating) by explaining them that by compromising on
dissuade clients from using UV (replace with aqua) as it's a colossal user of energy.
4. Use of LED or other such energy saving light sources in the factory.
5. Engaging with suppliers to teach/recommend the correct disposal procedure.
6. Fitting motion sensor light switches in corridors or where these is occasional movement.
7. Knowing what to use for which process - I have seen several converters using IR as a drying medium for aqua coating - this is just not necessary- plain hot air works well if there is a proper exhaust procedure. This could help save huge amounts in energy cost and help reduce your carbon footprint.
8. You can't completely eliminate usage of alcohol in older generation presses but with correct press setting it can surely be brought down by about 2-3 percent from the industry standard of 10.

How can the trial and error method of selecting the anilox roller in order to match a particular shade on a narrow web flexo press be replaced with something that is more accurate and precise? Your guidelines?
Sudhir Samant, consultant: Narrow-web flexo presses mainly used for converting Labels, are mostly printed by very stable UV ink system.
The introduction of precise and affordable measurement tools like spectrophotometers and colour-matching software, allow precise matching of colours in print packaging industry. This has also allowed ink makers to feed the colour information into ink dispensing systems that blend formulations that are closer to print target.
Printers should not do colour matching on press which is expensive in all respect and operator specific. Printers should utilise colour matching equipment and quality software to proof inks prior to press. This increases productivity and reduces waste.
Looking back: The thermal manufacturers like Kodak and Screen have made a good job to market thermal and by no means is it bad products. Likewise TN with violet. Today TN has the lion's share of systems out in the market place. But I think violet has come a long way since the first systems were installed. Is UVCTCP a step backwards for the industry?
Pranav Parikh of TechNova India: Any technology that helps a printer to step into a digital eco-system is relevant. What makes it sustainable though, is its simplicity, reproduction quality, consistency, uptime, openness, total cost-in-use, and most importantly a defined roadmap to green solutions. Violet, thermal and inkjet CTP technologies are constantly evolving with a seamless upgrade path to chem-free, water-free and process-free eco-friendly solutions.
Currently, the use of UV CTP technology is essentially confined to service bureaus with large plate volumes. They offer violet and/or thermal plates to quality conscious customers and UV CTP to the cost focused segment. In view of the inevitable emphasis by print-buyers and the government, coupled with ever-increasing demand for quality and fail-safe performance, many service bureaus are contemplating switching to chem-free thermal and violet CTP systems.
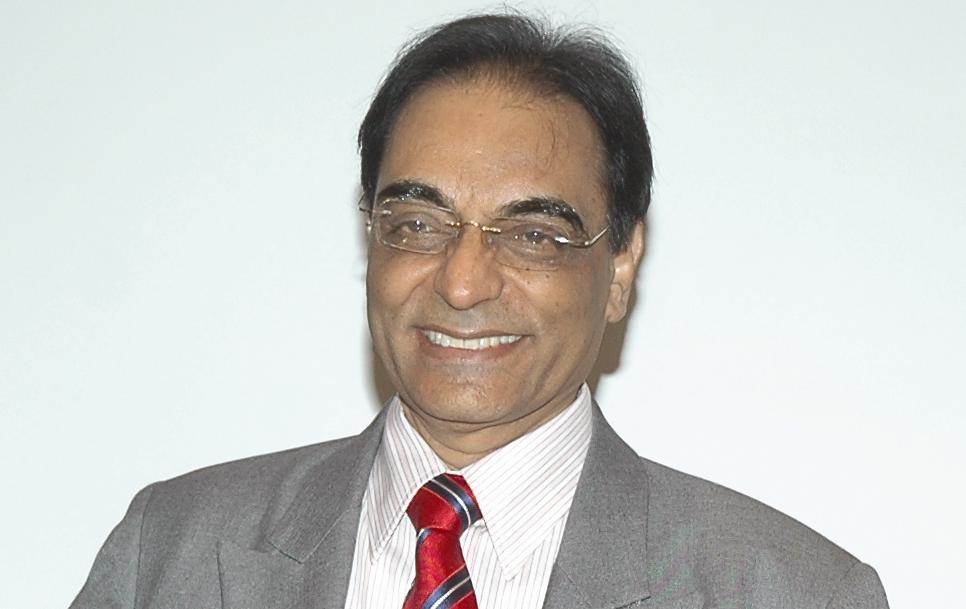
At the present time, there are very few print companies which manufacture HUV and LED. This makes the cost of inks expensive; which is a concern expressed by users. If more printers opt for these systems, would the prices of ink drop?
BS Kampani of Toyo Ink: The price would definitely depend upon the volumes and the regularity of the offtake. The price difference between a conventional UV and the HUV, LED could be in the range of 5 to 10% higher in the mid volume range usage.
In terms of printing, glue forms a very small part of the entire packaging process?
Nick Lehman, technical director, HB Fuller: Adhesives typically represent less than 0.2%. And, although adhesives may only contribute a small percentage of the total materials used in packaging products, they are playing a more fundamental role in delivering the enhanced functionality required for innovation, and meeting the changing demands of end users. In other words, typically with end-products, small parts play a big part in the functionality. Small by weight, but huge by application.
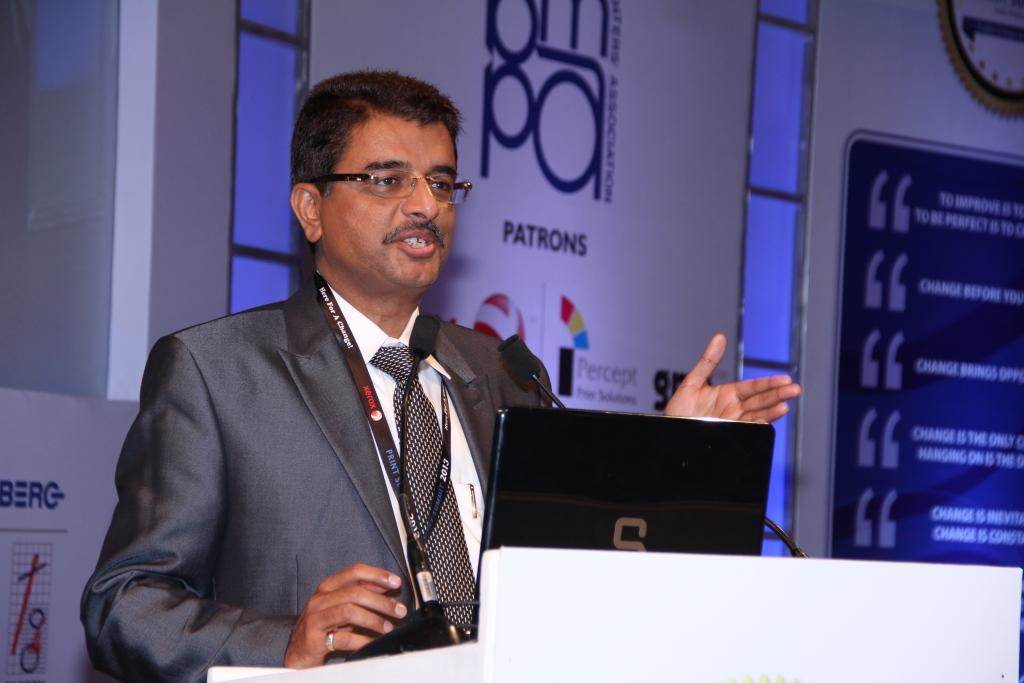
Is there a way to check that the lamps (for IR) are working effectively to know whether it is time to change these lamps? Recently we did a job without online coating and I felt the gloss factor increases by using the IR lamps.
Iqbal Kherodawala of Printline Reproductions: I believe there are strips available to measure the intensity of IR lamps, but technically, IR lamps are extremely redundant and it is a myth that they add gloss. They just heat the sheet enough for the varnish etc to immediately evaporate leaving a perceptive gloss only instantly. If you leave the sheet to dry reasonably enough, you will end up with the same gloss.
Since we are printing with solvent based inks and NOT heatset inks, IR should be used very judiciously. IR consumes power equal to the entire machine power and should be used ONLY to heat up the chamber so that the sheet gets a reasonably dry and warm area for travel. It is assumed that IR is effective for solids and for gloss, but this is not really proven. The solids will still give you problem if the ink is not a quickset ink. What the IR does is that it gives you a quick top layer drying leaving the inside masala still wet. This top layer also looks glossy and hence the perception.