The Hybrid shopfloor: Common post-press or bespoke finishing?
Many would say a dual-purpose finishing line on a hybrid shopfloor is a bad idea, as equipment designed for offset may not work for digital.According to others this is possible. The key is to train the operators. Rushikesh Aravkar considers the pros and cons
04 Jan 2017 | By Rushikesh Aravkar
In last five years, the Indian print industry has shifted from one crossroad to another. A few years ago, we deliberated whether digital will replace offset. Today, commercial offset printers understand that offset has been and will remain the workhorse, but there are areas where digital can become more profitable.
While a significant number of print firms have complemented their offset print operations with digital machines, it’s only a matter of time when other shopfloors too will see digital equipment reserve a place beside the offset presses. But then what about post-press?
As one school of thought goes, it is pertinent to have a dedicated post-press line to finish digital output; post-press equipment designed for offset may not be fit the bill. If one subscribes to this theory, adding a digital press is equivalent to setting up a separate print shop altogether, which translates to significant capital expenditure in the era of thinning margins.
Economically speaking, hybrid shopfloors, which deploy both offset and digital setups, are much more comfortable running a common post-press line. The digital output just streamlines into the offset workflow.
According to Pratik Shah of Mumbai-based PrintStop, the devil is in the detail. He says it depends more on the process of finishing than the printing process.
PrintStop deploys seven digital engines, a mix of Konica Minolta, Ricoh and Xerox, in the pressroom. The post-press consists of manual and semi-automated machinery – a Polar guillotine, a Welbound single-clamp perfect binder, a Champion thermal lamination machine, semi-automatic wiro punching and closing machines, a Morgana creaser and a Duplo DC-645 slitter-cutter-creaser, plus a few other smaller machines.
Even though it’s a digital-only print firm, Shah argues that PrintStop’s operation resembles a hybrid set-up. “We do have considerably large volumes, which are outsourced to offset firms. And we do finish a lot of this work in-house. From this perspective, we do have a hybrid line.”
At PrintStop, virtually all the bindery gear is used for both offset and digital work, says Shah. For example, outsourced offset and digital print are both guillotined on the Polar and bound on Welbound machine.
“What is more important is the mindset of the binding personnel who will cut the jobs. Traditional offset setups have binders who can’t cut 5-10 sheets jobs all day. They are more used to running standard programmes and larger job runs. We use the same perfect binding machine as well as the same lamination machine,” adds Shah.
“What again is important is the sensitivity that if it’s digital even a single sheet wastage is not affordable. Considering this, if someone has a Muller Martini saddle stitcher, he would be better off not running digital jobs on it because of the wastage. He would either prefer to have a small manual foot operated saddle stitcher.”
“If you think having a separate post-press setup for digitally printed sheets will save you money, it’s a myth. If you have considerable digital work it is important to train the mindset of the operators. The same machines can do the job. But, it would always help to have some digital finishing machines like a Duplo or a Morgana where each sheet needs to be unique,” adds Shah.
Going for bespoke
Meanwhile, some businesses are investing in bespoke digital bindery gear. When New Delhi-based Royal Offset decided to venture into digital printing in May 2016, it invested in a Xerox Versant 2100 and a Duplo DC 646.
The ISO 9001:2008 certified plant is equipped with a full-fledged pre-press house and consumes around 100 plates per day. In the pressroom, the book printing company has a Komori LS429 and a Ryobi 924. Last year, it installed a Stahl paper folding machine and a Polar automatic paper cutting machine.
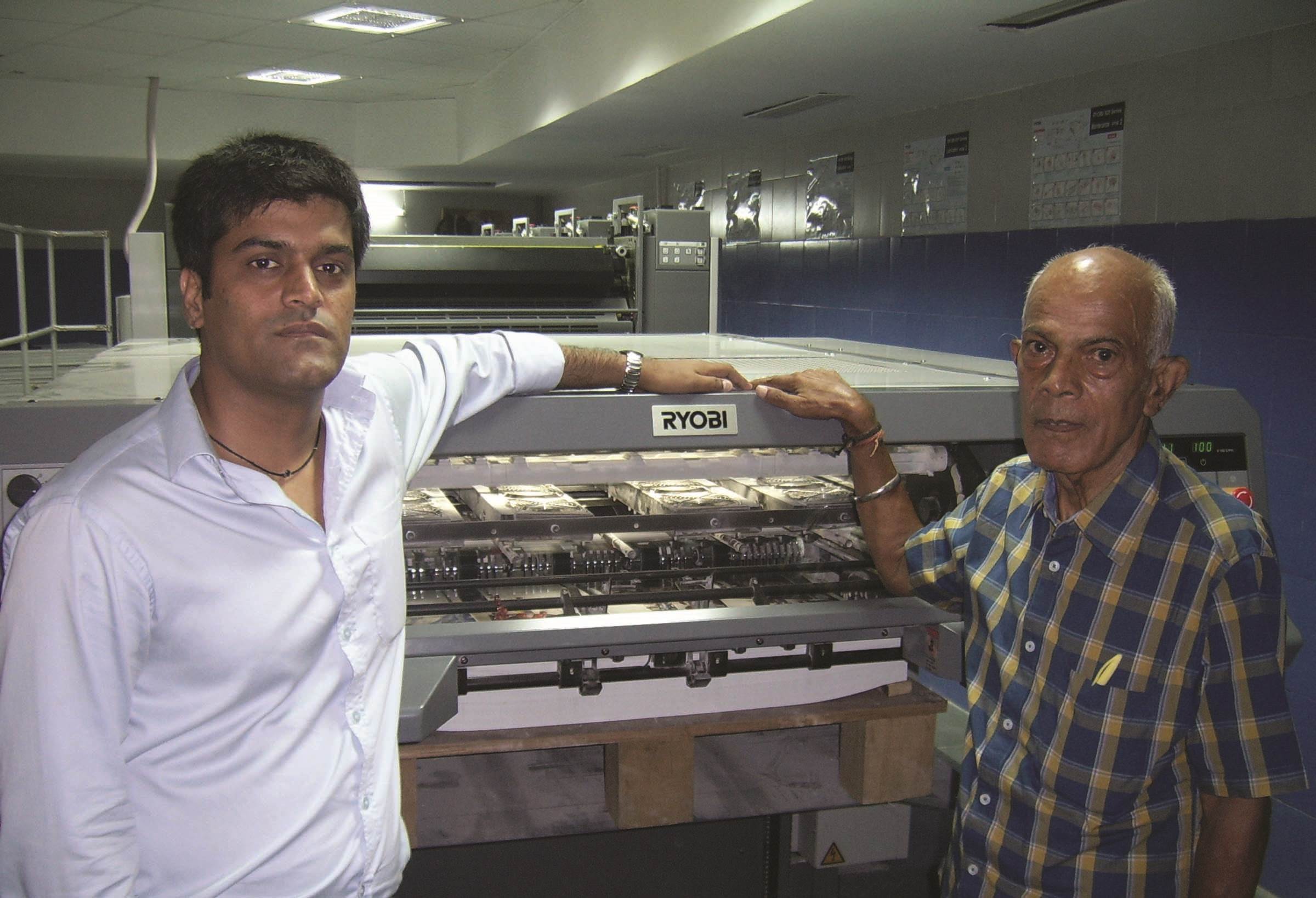
Vikas Arora (l): “The toner printed jobs need specialised finishing equipment to prevent cracking”
The owner, Vikas Arora, said offset and digital should be separate production lines entirely. “We see growth in short-runs,” he says, “The digital line complements offset and thus, we can offer books on demand to customers who need them. In the process, we are establishing ourselves as a complete solution provider for commercial and books printing.”
More than digital print, however, Arora believes finishing is an aspect that needs special attention. “Customers go to a digital printing facility because they need quick delivery, and if you do not have finishing equipment, then there is no benefit for customers. You will print fast but you will be stuck in finishing. So, a dedicated finishing kit is necessary,” he said.
Arora points out that the toner printed jobs need specialised equipment to prevent cracking on the edges during scoring and folding. “Sometimes, we pre-score the stock before we run it through the digital machines. In those scenarios, we’ll pre-score the stock and there’ll be no cracking, even if the colour goes right over the score.”
The Duplo DC 646, supplied by TechNova, slits, cuts, and creases both ways – horizontal and vertical, Arora finds it extremely effective with commercial digital work and the volumes relating to that.
Ajay Nagar of TechNova Imaging Systems, which supplies Duplo range of digital finishing machines in India, is a firm advocate of specialised post-press for digital and is sceptical about the efficacy of hybrid houses using dual-purpose bindery. He says, “There should be a dedicated finishing line for digital to handle different paper sizes, short-run jobs, and customised jobs, a wide range of applications and to serve print-on-demand. It is quite possible that all the digital jobs cannot be processed with the common post-press. Hence, having a separate finishing line works well. However, it also depends on the digital print volume. For an average of 400 sheets per day to be finished, a dedicated finishing setup is required and justifies the necessary investment.”
Embracing the challenges of digital print finishing
Market demand for short-runs, quick turnarounds, and variable data has driven more and more commercial printing set-ups to add digital printing capabilities. The process differences in digital printing and offset call for special attention when processing digitally printed sheets. Here’s what happens.
Offset inks versus dry toner: In the electrophotography-based digital presses powdered toner is fused onto the paper using heat and silicone fusing oil. Therefore, unlike offset process wherein the ink dries by absorption by the substrate, toner sits on the surface of the sheet. This difference can impact certain finishing processes. For example, the presence of fuser oil can cause issues with thermal laminating films, especially when you are laminating digitally printed solids. It cancompromisegluingandUV coating adhesion.
Static electricity: In the digital printing process, electromagnetic charges play a crucial role when toner powder is transferred from a charged drum to the paper. The resulting magnetic attraction manifests itself in the form of static cling, which can lead to sheets will stick to one another causing difficulty during feeding, collating and punching.
Paper: The paper used in digital printing is tweaked to allow for the proper fusing of toner. While uncoated and matte-finished papers will generally run fine, a gloss finish can cause toner to flake. This calls for special care during folding. It is recommended that digitally printed sheets must be scored prior to folding.
Toner cracking during folding can be influenced by the heat used in the fusing process. This paper tends to lose moisture due to the heat, leading to cracking. If the manpower is available, hand folding is recommended for smaller runs.
Saddle stitching is a popular binding option for many digital printing applications. It’s appropriate for thinner book projects such brochures and newsletters. One of the keys to the economy of stitching is its ability to be performed in-line with several ancillary functions. A post-press services provider that can gather sheets, stitch, fold and face trim inline will be able to offer the tight turnaround times that digital print applications demand.
Considering makeready
Offset finishing gear is generally designed to take care of large volumes of identical print but digital print runs are often not homogenous. Variable printing may require variable perfect binding with barcoding and several kinds of personalisation.
And then there are the makeready times, which are proficient for relatively longer runs of offset work running on conventional bindery kit. When a far shorter digital job is supposed to be processed on such machines, suddenly the makereadies are way too long. By contrast, a digital booklet maker can be set up in minutes.
At Akruti Offset, an offset-only operation, the run lengths have become shorter over the years and this necessitated that the firm added digital finishing machines to complement its raft of post-press equipment.
The Pune-based firm deploys a single-colour Heidelberg Sord, a four-colour KBA Rapida 74, and a four-colour plus coater Komori Lithrone S429, and in the post-press, it has a complete binding line with processes like lamination, spot UV, die-cutting, section sewing, and other machineries like Stahl folding machine, Sheridan automatic booklet maker, Welbound PUR perfect binder, Morgana Digifold, and Stago creasing machine.
“Digital finishing kits like Morgana, Stago and Sheridan enable my bindery to be flexible enough to quickly handle short-run, multiple jobs, even though printed on offset,” says Sahil Rao of Akruti.
Rao believes that a common post-press for a majority of the hybrid set-ups can work especially when you have short-run offset jobs. “You can combine most of the primary machines like the cutting machines or little robust automatic creasing and folding machines but when it comes to specialised finishing, I will advise having a separate line to get the most from your machines,” says Rao.
Akruti Offset specialises in corporate brochures, magazines, annual reports, and coffee-table books. When it comes to special treatments like spot UV, textured UV, foiling and most of the binding processes it’s always better to have a dedicated set-up for digitally printed sheets, recommends Rao. “It will surely save you some money in a long run if you consider the time and overheads like manpower, electricity, and wastage, etc.”
Rao argues that if you are having an offset folding machine which needs a lot of makeready time and need to run few sheets to get the fold at the desired location then it won’t be economical to do a digital job on such a machine as you will be wasting a lot of sheets during makeready.
“The makeready time for digital machines is negligible; you don’t need to constantly run the machine to get the best out of it. There is hardly any sheet wastage compared to offset-oriented machines. Since most of these machines are compact and easy to use, you can train your operator to use multiple machines.”
Nagar says, “A digital job has an average print impression of 20-25 sheets and each job is different. The offset post-press may not justify the running cost for such few impressions every time. Hence, having a digital post-press system will incur an initial capital cost, but the running cost will reduce and time will be saved.”
Nagar makes a valid point that it not only makes operational sense but also makes business sense. “The bespoke post-press will also complement the printer’s existing business line. His printing volume will increase due to faster turnaround. His customer retention will increase as he will provide ready finished product. And as he is using dedicated finishing line the results will be very accurate and precise.”
Is outsourcing an option?
It’s a fair question, whether outsourcing is an option.
Rao says, “I don’t think outsourcing post-press for digital is a better alternative. It does not save you any money since all your jobs have a very short run-length. The post-press plays a very crucial role today. It’s a risk to depend on someone else for this, as it can entirely ruin your job if not done properly.”
Nagar observes, “Outsourcing depends on many factors: the type of customer, location, kinds of jobs he processes, accuracy and precision expectation, does he control the entire process and most importantly what is the productivity that he delivers. If the print volumes are very less and one has more economical options available outside his door, then outsourcing is a good idea. But at the same time, you are hampering your growth.”
However, Sheth is sceptical of outsourcing as a digital finishing solution. “Outsourcing costs impact final print costs, affecting competitiveness. Having the capabilities in-house reduces turnaround times and cost.”
“It should be noted that the toner printed jobs need specialised equipment to prevent cracking. If you use traditional roller creasing, the toner will crack on the digitally printed media,” says Nagar. “In such cases, it is recommended to use good quality pressure creasing which uses male-female die technology like Duplo devices. While folding, the grain direction of the paper needs to be considered before creasing and folding.”
But in shops where finishing volumes fluctuate considerably, hybrid products such as the Morgana Pro range, which includes the DigiFold Pro and the DocuMaster Pro booklet maker, and Duplo’s DC 616 and DC 646 are capable of finishing both offset and digital products.
Hybrid businesses are generally after entry-level kit for digital because they have identified the need for specialised digital finishing but do not want to spend huge amounts on that side of their finishing.
Today, a wider range of digital finishing kits are available, and they are built with new functions for both offset and hybrid use. Print firms do not necessarily need to segregate offset and digital finishing but the key is to identify exactly which processes need digital-only finishing.
Simple solutions
Parag Shah of Hi-Tech Systems PFE, has supplied more than 1,600 print finishing machines to 750+ customers. Hi-Tech represents a host of finishing equipment manufacturers from Kisun, Bacciottini, Onglematic, Cyklos, Rhinotuff, and Opus among others.
Shah says, “There are a surprising number of digital printers opting for the flexibility, affordability and ease of use offered by manual and table-top machines. Take photo album specialist SRK Creative. It profitably deploys a range of simple machines from Hi-Tech’s stable including creasing machine, back-to-back pasting, UV coater, centre taping etc for its digitally printed products.”
It’s a similar story with the Hi-Tech’s other clients like Mumbai-based Laxmi Xerox, Indore-based Bahety Copy Centre, Jaipur’s Titu Thesis Center, Bengaluru’s Printo and Chennai’s Computer Prints among others.
“For certain jobs, instead of adding unnecessary automation with increased capital cost, it is easier and quicker to do it by using hand-fed equipment. You cannot find a better way to earn ROI.”
Case-study: Avantika Printers
New Delhi-based Avantika Printers has an all-inclusive digital printing set-up comprising of pre-press, digital printing, screen printing and post-press, while offset printing is outsourced. Avantika is one of the few print firms in India who have opted for finishing units that go inline with the digital printing machine.
Himanshu Pandey (in the photograph above), the second generation director at Avantika, believes that for certain kind of jobs you could save significantly on operational costs with these inline finishing units supplied by digital printing equipment manufacturers. Avantika has invested in an inline stapler on Canon C7010VP and a folding unit on Oce TDS 750.
Pandey explains, “We have a client who needs technical drawings of A0, A1, A2, and A3 size to be printed and folded in ISO standard A4 size with a hole punched and back tape pasted on it for insertion in a file folder. We print this job on Oce TDS 750 with inline folding unit. Using this machine our job time and operational cost reduced by 50% as compared to doing it on an offline folder.”
However, one can leverage the inline finishing units only for standard print jobs. There are certain limitations to it. Pandey says, “Suppose you go for a line that does stitching and cutting. Since these units have to be inline with the printing machines, they consume lot of space in your printroom but can do only limited type of jobs restricted by the attachments used on the machine. However, in the case of offline machines, one can invest in small or big equipment depending upon one’s capacity and do various kind of jobs not limited as standard inline solutions.