Following Uflex from Kentucky to Dusseldorf
Who doesn’t know flexible packaging giant Uflex? What is more interesting, however, is how the Noida-headquartered company successfully integrates the different aspects of packaging to offer a complete solution. Thus, the company manufactures packaging films, the base material for packaging, and then, to fill the package with actual products, the company manufactures converting, filling and sealing machines.
Recently, PrintWeek India had an opportunity to take a close look at Ufl
01 Jul 2016 | By PrintWeek India
A single winder’s capacity is 72,000 metres. It depends on the outer diametre of the roll. In weight, it can be a jumbo of 10,000 kg
The core team of Flex Films (USA), from left, Praveen Murlidharan, responsible for IT; RatneshwarJha, responsible for accounts and finance; Wayne Morris, chief financial officer; KK Sharma responsible for production and Deepak Chopra, who take cares of sales and marketing
A single winder’s capacity is 72,000 metres. It depends on the outer diametre of the roll. In weight, it can be a jumbo of 10,000 kg
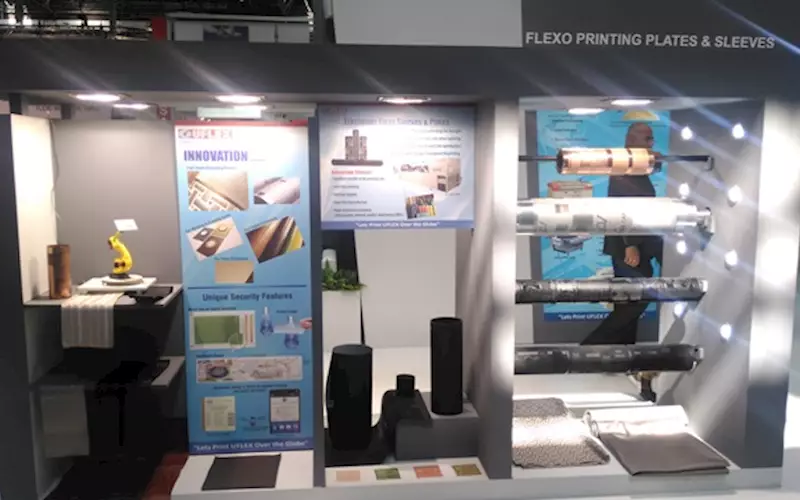
Uflex Elastomer flexo printing plates and sleeves showcased at Drupa 2016
Thickness of the films produced at the US plant ranges from eight to 50 microns
The Electronic Line Shaft (ELS)-based rotogravure printing machine Ultima on display at Drupa 2016
With a production capacity of 30,000 MT per annum, the plant is supplemented by a plasma-enhanced high-barrier vacuum metalliser that can produce around 11,000 MT of metallised film annually
More than 10-metre-long heating chamber stretch the film more than eight metres width. These heating chambers run electric heaters
More than 10-metre-long heating chamber stretch the film more than eight metres width. These heating chambers run electric heaters
More than 10-metre-long heating chamber stretch the film more than eight metres width. These heating chambers run electric heaters
Films on jumbo cannot be used directly because of its big size (more than eight meters). Slitters cut films into sizes demand by the customers
The softening temperature of the chipsis 69 degrees Celsius and the melting temperature is 240-250 degree Celsius
The warehouse of the US plant
The US plant houses an 8.7 metre BOPET film line that runs at 500 metres per minute
Here is the first time when you can see the film in physical form. This is the base form of film and it will be stretched more than three times through heating process. Heat is generated by electric heaters
Uflex solvent-less laminator - standard S machine
At the US plant, workers come from different backgrounds, geographies, ethnicity
The quantity depends on diameter of the rolls. A jumbo roll takes three hours to be fully loaded
J Kampf slitting machines provide films on customers’ need
Flex Films (USA) manufacturers films on demand and follows a zero inventory model
White chips are made of recycled material will be used for film manufacturing again with a mix of virgin white chips
Chilling system with cold water maintains temperature of around 12 degrees Celsius on the surface of the roll
Flex Films follow a strict and regular chart of maintenance which help the company to produce films flawless
The US plant houses an 8.7 metre BOPET film line that runs at 500 metres per minute
.