When designing a package means building a shield
To ship its Accucraft i250+ 3D printers across the country, Navi Mumbai-based Divide By Zero Technologies came up with a sturdy package, complete with multiple layers, air bubble film, EPE foam, seven-ply corrugated box and a wooden crate. Yet, when the product underwent damage during transit, the company decided to go back to basics. In this case study, Rushikesh Aravkar deconstructs how Divide By Zero came up with an alternative packaging solution
30 Jun 2017 | By Rushikesh Aravkar
Some year ago, when Dutch bicycle manufacturer Vanmoof started shipping its ready-to-ride bicycles to its customers, the product delivery turned out to be a nightmare. Customers complained that the bicycles packed in big cardboard boxes were damaged during transit. It appeared that logistics companies tend to drop and bash and crush bicycle boxes during loading and unloading.
Back home in Navi Mumbai, a desktop 3D printing machine manufacturer, Divide By Zero Technologies, which ships its locally made Accucraft i250+ 3D printers across the country, was facing similar customer complaints of damaged deliveries. In one instance, an Indore-based customer reported dented corners caused due to abrasion and heavy impact caused bend in gantry.
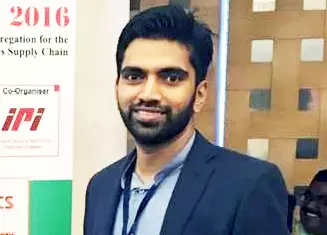
“In some cases, the machines were insured, but the loss of time in bringing back the damaged printer and close the deal was enormous. There were many cases where the machine was not insured and the entire cost of damage, and bringing back the damaged machine was borne by the company. We desperately needed a solution,” says Swapnil Sansare, CEO and founder, Divide By Zero Technologies.
Both the cases highlight one important aspect of packaging – its transport-worthiness. Anticipating bumpy rides, rains, hot summer and bone-chilling winter, dust and dirt, rough handling and whatnot, a package must build a shield strong enough to safeguard the product until it reaches its destination. This is the basic description of a packaging engineer’s job.
Back in The Netherlands, the Vanmoof team brainstormed. They hit upon the idea that couriers would be more careful if they knew the package contained something more precious than bicycles. The bicycle boxes were exactly the size of a huge flatscreen television. So Vanmoof decided to print a television on the boxes. The idea worked. In the US, the number of complaints for damaged goods reduced by 70 to 80%.
While smart thinking saved the hard work for packaging technologists at Vanmoof, Divide By Zero went back to basics to reengineer its packaging. Soon a fresh packaging engineer, Aparna Vinod, came onboard to build the shield for Accucraft i250+.
When Aparna, a final year student of Printing and Packaging Technology department of SIES GST, first met Sansare in February 2017, she was looking for an internship opportunity, a final phase of her degree education, and Sansare was in need of a packaging solution. Aparna was tasked with designing a sturdy transport package. How fortunate, she thought, as she rolled up her sleeves to engineer a real-life packaging solution.
Making a strategy
Aparna says, “Since Accucraft i250+ is a sensitive electronic component which is also expensive, damage reduction or elimination becomes mandatory. Reworking the packaging is the way the company decided to go, primarily due to damage concerns. However, ease of handing for operators as well as customers and possible reduction in costs was yet another reason to redesign the transport packaging.”
The first step was to study the product, its physical aspects, packaging and the specific damages that it faced.
The Accucraft i250+ is a FDM desktop printer of a built size of 300x250x200 mm. It weighs 35 kg and is a fully enclosed 3D printer with a body made up of sheet metal. Its external dimensions are 17.5x17.5x25.5-inches. The sheet metal body of the 3D printer has sharp edges. The top of the printer has a PMMA sheet for viewing the print. In the same way, the front panel has hinges on it to hold an acrylic door that can be opened for accessing the built platform.
Aparna says, “The existing packaging had multiple layers. All ancillary equipment and consumables were placed inside the machine. Air bubble film (cling on) and roll of 8mm EPE foam was cut and used as filler inside the machine to restrict movement of the items inside.”
The machine was then wrapped with 4-5 layers of the same bubble film and two layers of 8mm thick EPE foam. It was then placed inside a seven-ply 120gsm BB-fluted corrugated box. The corrugated box was then taped and strapped with a PP strap and was wrapped once again with the air bubble film. It was then placed inside a wooden crate. The top of the box was nailed and the markings for the crate was printed and taped onto the box.
On the face of it, this looked like a strong package, but in many cases, it couldn’t protect the product from damage. Aparna’s evaluation of the customer complaints revealed that in most cases, the acrylic spool cover was found broken inside the machine. Secondly, the corners of the sheet metal enclosure had abrasive marks and dents. And finally, the gantry was dislocated or bent in several cases.
Aparna explains, “The sharp corners of the machine that were damaged are likely due to the impact of corner drops during handling of the package. The gantry was probably damaged due to force on corners during an edge drop that caused change of diagonal dimension of the machine. This led to the gantry frame coming out of its slot and bending eventually.”
The acrylic spool covers were placed over the built platform in assembled form and the only separation between the covers and the extruder was filled in air bubble film and foam. However, on evaluating the air bubble film, it was found that the bubbles were broken, which created a gap inside the machine leading to movement of the spool cover and breaking due to impact with sheet metal or with each other.
On the basis of this investigation, the team decided to set parameters of the new packaging. First, the new package should sufficiently protect the edges and corners of the machine. It should be moisture and waterproof, light in weight and easy to handle. Also, one of the important conditions was that the packaging material should be easily available in low minimum order quantity (MOQ).
Devising a solution
Now the most critical part was to identify the packaging material. “To select cushioning that is efficient was the most critical part of this assignment,” says Aparna. “With the aim to provide cushioning between the product and the corrugated box, expanded polyethylene (EPE) or expanded polystyrene (EPS) foam were considered. Another possibility was to immobilise the 3D printer by using strong corrugated board internal fitments. However, later on EPE foam was selected over EPS foam and CFB fitment.”
The selection of EPE foam was logical. The existing packaging had used EPS foam in form of sheets in between the product and the CFB box. This foam sheet was of low density EPS and therefore, problems such as dusting and creep were observed during unpacking by the client. “This was probably due to abrasion between the EPS sheet and the sharp edges of the machine’s body,” adds Aparna.
Secondly, high-density EPS moulded caps although cheaper than EPE foam are not available in small quantities. Even though, corrugated internal fitment was a good option to immobilise the product and a cheaper way of cushioning, sourcing custom-made corrugated fitments in smaller quantities was difficult.
In order to design the EPE foam, Aparna referred to IS 10106-1-4, 2005 standard. Considering the gross weight of the product, type of handling, a drop height of 750mm was selected as per the standard. And fragility factor range of 40 to 60G was set depending up on the degree of fragility.
“The maximum stress acting on the product was calculated and a graph of Static Stress (kg/cm2) versus G-Factor for non-cross-linked EPE foam of density 35 kg/m3, thickness 70 mm and drop height of 750 mm was referred from the IS standard,” explains Aparna. “Basis this calculation, we derived three different configurations of foam structure and placement inside the package.”
- Configuration 1: End Caps (top and bottom) made of thickness 70 mm and depth of 100 mm on z-axis and spanning the entire printer on x and y axes.
- Configuration 2: Cushion on edges of thickness 70 mm with 100 mm depth on z-axis and 150 mm on x-axis, while spanning the entire printer on the y-axis.
- Configuration 3: Cushion on all 8 corners of thickness 70 mm and expending to 13 mm on all the axes.
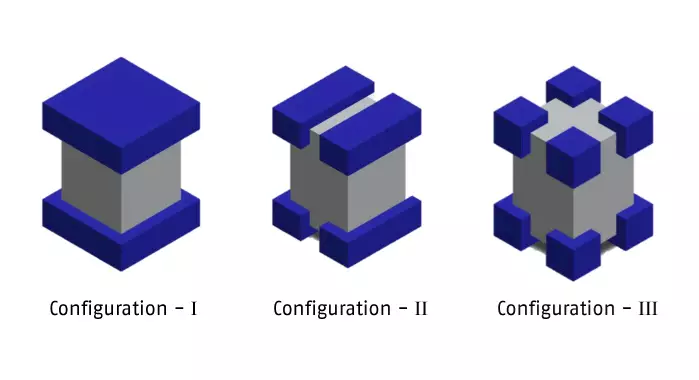
The R&D head at Divide By Zero selected the first configuration because the 3D printer being an expensive product, keeping the static loading on the lower end was preferred.
The next step was to design the corrugated box. “The existing box configuration was 7-ply 120gsm B-flute. We spoke to several corrugated box vendors but only one agreed to supply quantity as low as 20 boxes. That too, he could supply only 140gsm Kraft and B-flute configuration. So, we decided to test with the available configuration of RSC type box,” says Aparna. To reinforce the box, 3mm angular board was fitted at the corners.
With proper cushions in place, Aparna was confident that the wooden crate in the existing package can be eliminated. It was decided to put this new packaging to test. Aparna adds, “We used the original product for transport testing of the new packaging. The ancillary components including the acrylic spool cover were placed inside the machine wrapped with air bubble film like similar to the existing packaging. The whole new package was tested against vibration, horizontal impact, rolling test and drop test.”
It was observed that the cushion foam was intact without any puncture or tear and thereby no damage of gantry and other critical machine components was reported. The acrylic spool cover was broken and minor bends were observed on sheet metal. The air bubble film around the acrylic spool cover had all broken bubbles and the corrugated box was torn at the edge due to the drop test holding clamp (human error).
Working on these observations, the packaging configuration was tweaked slightly. “We developed a new toolkit for ancillary materials that fits exactly on the inside of the machine. With this the acrylic spool cover was sent in lay-flat condition,” she says.
Secondly, the box design was changed from RSC to a three-piece box (top-sleeve-bottom) to eliminate the minor bends as it provides double 7-ply boards at the edges. “Thus, the angle boards were also eliminated. It enabled ease of handling so that during packing the personnel needn’t pick up the machine to the height of the box,” she adds.
With the revised configuration, the minor loopholes were eliminated and a robust packaging was put in place for Accucraft i250+. Not only this, the resulting new packaging was cheaper than the existing package as it eliminated the wooden box. Secondly, the total weight of the package was also reduced and logistic costs were also minimised.
Comparison of old and new package
Comparison of old and new package |
||
Parameter |
Old Package |
New Package |
Ease of assembling |
Lesser |
Greater |
Marking and Labeling |
Printed A4 paper stuck on box |
Screen printed on box |
Branding |
None |
Logo screen printed on top cap |
Weight |
Approx.45 kg (Higher due to wood) |
Approx. 40 kg |
Ease of opening- Customer end |
Nails on box need tools to open |
No tools required |
Cost of packaging |
Rs 1,402 |
Rs 870 |
Volumetric Wt. (Considered for shipping as chargeable weight) (surface charges) |
110.12 kg |
105.45 kg |
Cost of Shipping |
Rs. 550.6 |
Rs. 527.25 |
Costing of old package |
||
Material |
Quantity/ package |
Cost (Rs.) |
Wooden box |
1 |
900 |
CFB Box- RSC |
1 |
152 |
EPE Foam Roll |
3 metre |
270 |
Air Bubble Roll |
5 metre |
50 |
Tape |
1 roll |
30 |
Total Cost (Rs.) |
1,402 |
Costing of new package |
||
Material |
Quantity/ package |
Cost (Rs.) |
CFB 3 Piece |
1 |
210 |
EPE Fitment |
1 set |
500 |
EPE Foam Roll |
1 metre |
90 |
Air Bubble Roll |
4 metre |
40 |
Tape |
1 roll |
30 |
Total Cost (Rs.) |
870 |