Exploring possibilities to die-cut corrugated board without using a creasing system
In the case of die-cut packaging a creasing system should be always used at least with the flute. When converting laminated E and B-flute materials it is practically impossible to do without a creasing system.
23 Jan 2017 | By PrintWeek India
The conversion of corrugated board is subject to a special sort of problem, for it is not possible to predict whether the creasing process will take place in the valley or the tip of the flute. Due to the structure of the material this will continually change during the die-cutting process. So if you do not use a creasing matrix you run the following risk; as soon as a creasing rule runs into the tip of a flute, the required crease will not occur in the predetermined position but the material will take the way of least resistance, i.e. the creasing will be created in the adjoining valley. This may happen both on the left and on the right of the requested creasing position. On the one hand this will result in a poor creasing and on the other the phenomenon is noticeable, that the packaging is no longer dimensionally accurate, i.e. due to the incorrectly positioned creases single parts of the packaging become longer while others get shorter. This is not only an optical or technical defect on the packaging but it is often the reason for considerable disruptions on folder- gluers as well. Too large a variation in the dimensions cannot be compensated for folder-gluers and thus machine stoppages are inevitable.
Of course, the use of a creasing matrix does not eliminate the phenomenon of valley and tip of the flute. In this case, too, we still have the problem that creasing rules are to run partly into the valley and partly into the tip of the flute. The use of a creasing matrix, however, ensures that the creasing, even if its quality may vary, is always located in the required position. Here the creasing channel serves as a guide edge for the creasing and forces the material to become creased in the required place. Thus dimensional stability of the packaging can be guaranteed and the described problems occurring in the further processing are eliminated, Of course, the use of a creasing matrix does not only considerably improve the creasing quality but it involves other advantages too, i.e., the mechanical functionality is improved and the creasing of the packaging is optically better marked.
Another essential factor in the processing of corrugated board is the die-cutting direction. Now as before, one can often see that corrugated board is principally die-cut from the inside, i.e. with the printed side down. When working with inline machines such a processing method is indeed unavoidable, as in-line machines are equipped with an integrated flexo printing unit. These machines have the flexo printing unit underneath the sheet transport mechanism, so that the side to be printed is the bottom side of the transported sheet. Consequently, the sheet cannot be turned prior to the die-cutting process.
In an extensive series of tests the die-cutting results obtained when done from the inner side and when done from the printed sides were compared to each other. This comparison produced the following result: when bending the material up to 90 degrees there is practically no significant difference in the expenditure of force, no matter whether the material was die-cut from the inner or the outer side. However, if the material is to be bent by 180 degrees, which is a prerequisite for processing on a folder-gluer, things look quite different. The expenditure of force required in order to bend material die-cut from the inside by 180 degrees is approximately four times as high. This results in a considerable loss of performance in the further processing on folder-gluers and in an increased risk with regard to a tearing of the cover sheets. Therefore, whenever it is possible, it should be ensured that corrugated material, too, is die-cut from the printing side.
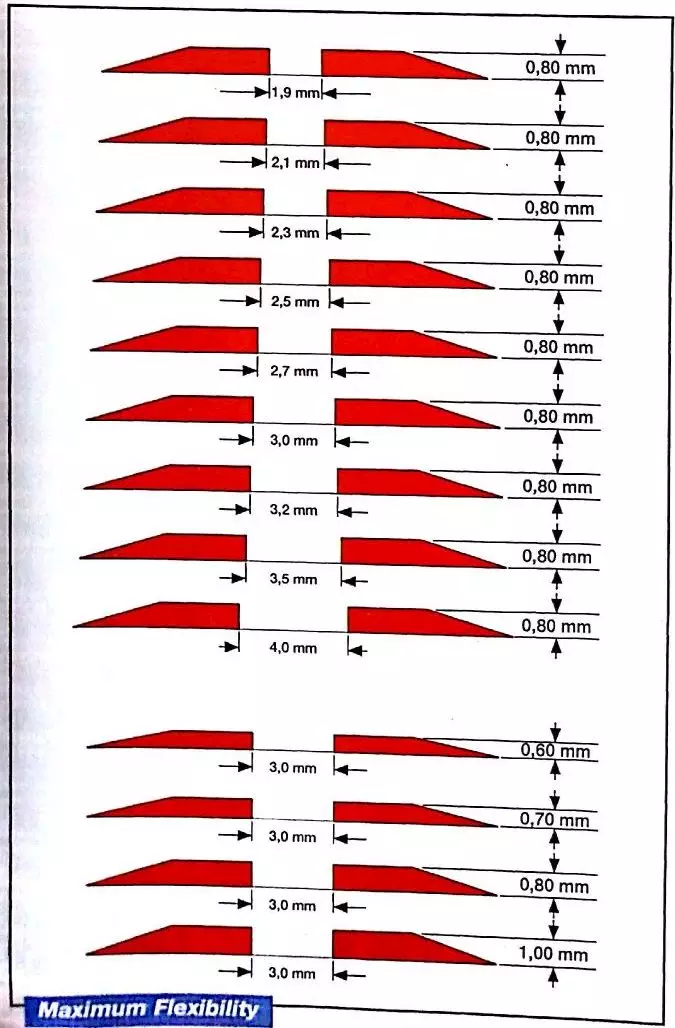
At any rate, when selecting a creasing system, one should take care that this system offers a maxi mum of flexibility. Particularly when converting corrugated board the influences resulting from the quality of the material play an important role for the machinability. If the material comes directly from the corrugated board plant, it is to be expected that it still has a high moisture content, which means that the material features a good creasability. When stored for a longer period of time, however, this material will dry out; then an impaired creasing ability is noticeable. In addition to this, due to the fact that recycled paper is increasingly used as liner material there occur significant quality variations and varying fibre lengths in the cover sheets. A creasing system must be able to react flexibly to these quality variations as well, i.e., it happens quite often that the creasing channel depths or widths have to be adapted. That means, however, that a system has to be used which guarantees that various creasing channel widths of the same depth or various creasing channel depths of the same width are available.